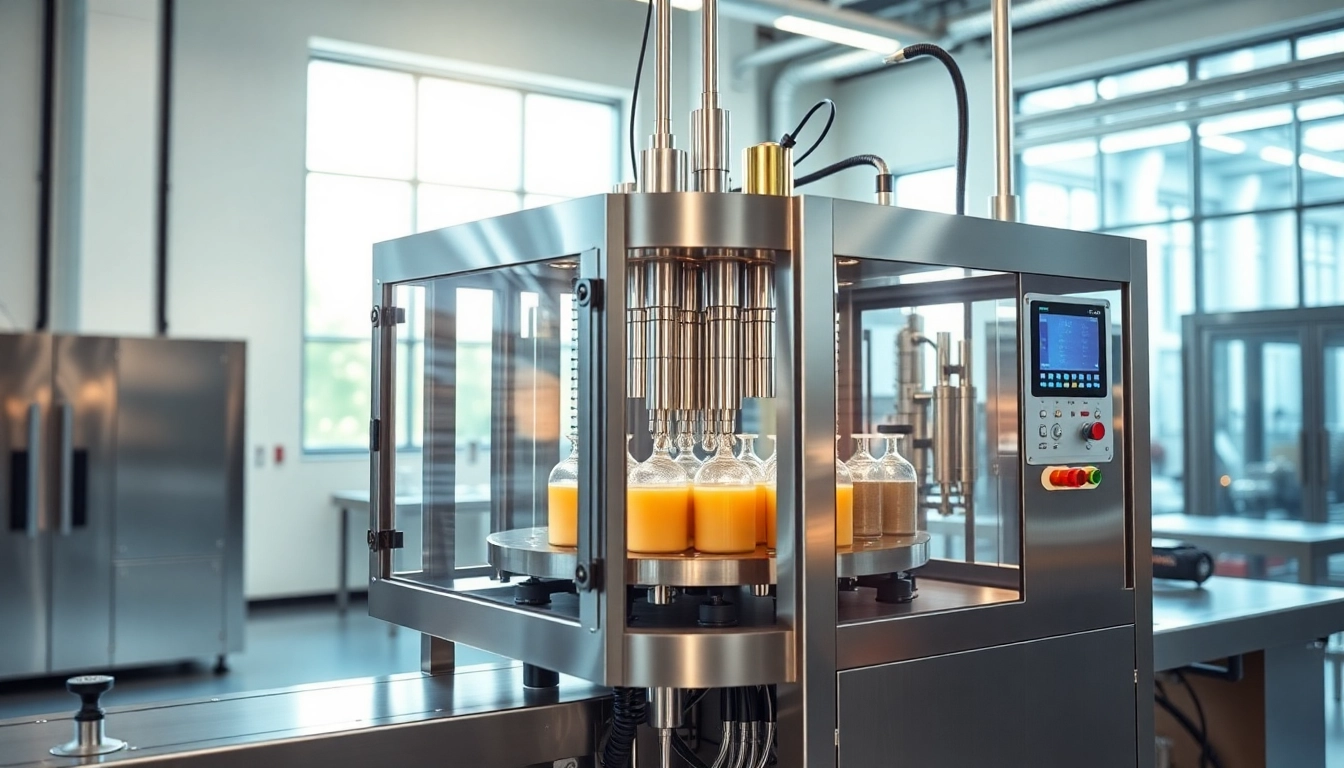
Understanding Liquid Packaging Machines
What Are Liquid Packaging Machines?
Liquid packaging machines are specifically designed equipment utilized to package liquids into various types of containers. They function by filling, sealing, and sometimes labeling products such as sauces, beverages, or industrial fluids efficiently. The importance of these machines cannot be overstated; they streamline the packaging process and ensure that products are packaged securely and hygienically, reducing the risk of contamination and ensuring compliance with industry standards. As a Liquid Packaging Machine Supplier, sourcing high-quality machinery is essential for businesses aiming to improve their operational efficiency.
Types of Liquid Packaging Machines
Liquid packaging machines come in various types, each tailored to specific product characteristics and packaging requirements. Common types include:
- Filling Machines: These machines fill containers with liquid products at high speeds. They can be classified further into categories such as volumetric, gravimetric, and pressure filling.
- Sealing Machines: These devices seal filled containers to preserve product freshness and prevent leakage. Sealing can be achieved through heat, ultrasound, or pressure.
- Labeling Machines: Following filling and sealing, labeling machines ensure that products are correctly labeled for branding and compliance with regulatory requirements. They apply stickers, prints, or embossed labels onto containers.
- Packaging Lines: Integrated systems that combine different types of machines to form a complete packaging solution. This includes everything from filling to sealing and labeling in one automated line, enhancing process efficiency.
Applications in Various Industries
Liquid packaging machines serve a multitude of industries, each with unique requirements and challenges:
- Food and Beverage: In this sector, packaging machines handle liquids like juices, sauces, and dairy products. They ensure hygiene, extend shelf life, and maintain taste and quality.
- Pharmaceutical: Packaging in the pharmaceutical industry demands high precision and safety standards. Liquid packaging machines for pharmaceuticals are designed to minimize contamination risks while ensuring accurate dosing.
- Chemical: Chemical liquids often require durable packaging solutions. Packaging machines here must withstand corrosive substances and abide by safety regulations.
- Cosmetics: The cosmetics industry utilizes liquid packaging machines to efficiently fill and package products such as lotions and oils, enhancing aesthetics while maintaining product integrity.
Choosing the Right Packaging Machine Supplier
Key Factors to Consider
Selecting the right liquid packaging machine supplier is crucial for operational success. Key factors include:
- Product Range: A diverse product range indicates the supplier’s capability to meet specific packaging needs, whether you’re looking for standalone machines or complete packaging systems.
- Customization Options: The ability to tailor machinery for specific requirements, such as container size or production volume, offers significant advantages in operational efficiency.
- Technology and Innovation: Suppliers that leverage the latest technology in automation and connectivity help improve manufacturing processes and reduce downtime through predictive maintenance and data analytics.
- Lead Time and Production Capacity: Understanding the typical lead times for machines and the supplier’s production capacity is vital to ensure that your operational timelines are met.
Evaluating Supplier Credentials
Assessing a supplier’s credibility is essential for ensuring that you partner with a reliable source. Consider the following:
- Experience: Suppliers with a proven history in the industry are usually more adept at handling challenges and understanding customer needs.
- Certifications: Look for certifications that demonstrate compliance with safety and quality standards, such as ISO certifications, CE marking, or FDA approvals.
- Customer Reviews: Engaging with past clients or reading online reviews can provide insights into the supplier’s performance, product reliability, and after-sales support.
Importance of After-Sales Support
After-sales support is a critical factor that often distinguishes a good supplier from a great one. Key aspects include:
- Installation and Training: Comprehensive installation services alongside operator training can significantly enhance productivity and reduce operational errors.
- Maintenance and Service Agreements: Ongoing maintenance agreements ensure that your machines stay in optimal working condition, minimizing downtime.
- Technical Support: Accessible technical support helps in resolving any arising issues quickly, keeping production lines running smoothly.
Benefits of Advanced Liquid Packaging Technologies
Increased Efficiency and Productivity
Advanced liquid packaging technologies enable companies to automate and optimize their production processes significantly. This leads to increased efficiency through:
- Faster Processing Times: Automated machines can fill and seal products much quicker than manual processes, reducing bottlenecks in production.
- Reduced Labor Costs: By investing in automated solutions, businesses can minimize labor costs while reallocating human resources to areas that add more value.
- Higher Output Rates: Continuous operation of modern machines increases overall production capacity, meeting rising market demands.
Cost-Effectiveness and ROI
Investing in advanced liquid packaging solutions translates to long-term cost savings and returns on investment (ROI) through:
- Energy Efficiency: Newer machines often use less energy compared to older models, leading to lower operating costs.
- Minimized Waste: High-precision filling machines reduce product waste, ensuring that resources are utilized efficiently.
- Lower Maintenance Costs: High-quality machines tend to require less frequent and less expensive repairs, contributing to overall savings.
Enhanced Product Quality and Safety
Modern packaging technologies not only boost efficiency but also improve product quality and safety through:
- Consistent Quality: Automated filling and sealing processes enhance the consistency of product quality, ensuring that each unit meets standards.
- Compliance with Regulations: Advanced machines incorporate features that assist in meeting stringent regulatory requirements regarding food and drug safety.
- Enhanced Shelf Life: Effective sealing methods ensure that products are protected against contaminants and environmental factors that could shorten shelf life.
Case Studies: Successful Implementations
Food and Beverage Industry Success
A leading beverage company implemented state-of-the-art liquid packaging machinery to streamline their production line. By switching to an automated filling system that adjusts fill levels based on real-time data, they improved production speeds by over 30% and reduced waste by 15%. Customer feedback indicated enhanced freshness and quality, ultimately boosting sales.
Pharmaceutical and Chemical Applications
In the pharmaceutical sector, a company faced challenges with contamination and inefficiency. By investing in a fully automated liquid filling line that adhered to cGMP regulations, they not only secured their compliance with strict safety standards but also reduced labor costs significantly. The enhanced accuracy in filling dosages led to a remarkable decrease in recall incidents.
Custom Solutions for Unique Packaging Needs
A cosmetic brand specializing in organic products required a unique packaging solution to cater to multiple product formats. By collaborating with a flexible packaging machine supplier, they developed a line that allowed them to switch between different sizes and types of containers seamlessly. This adaptation resulted in a 25% increase in product offerings, ultimately expanding their market reach.
Future Trends in Liquid Packaging
Sustainability and Eco-Friendly Innovations
As consumer demand for sustainable packaging solutions grows, liquid packaging suppliers are focusing on eco-friendly technologies. This includes using recyclable materials, biodegradable packaging, and designing machines capable of handling these materials efficiently. Suppliers that innovate in sustainability enjoy competitive advantages and meet increasing regulatory pressures.
Smart Packaging Technologies
Leveraging IoT (Internet of Things) technologies, smart packaging machines are emerging, enabling manufacturers to monitor and optimize their operations through data analytics. These technologies minimize downtime and enhance predictive maintenance, allowing for seamless operation and improved productivity.
Challenges and Solutions in the Market
Despite its advancements, the liquid packaging market faces challenges such as fluctuating raw material costs and increasing trade regulations. Suppliers that embrace agile manufacturing practices and enhance their supply chain strategies can navigate these issues effectively, ensuring stability and growth in an ever-evolving market landscape.