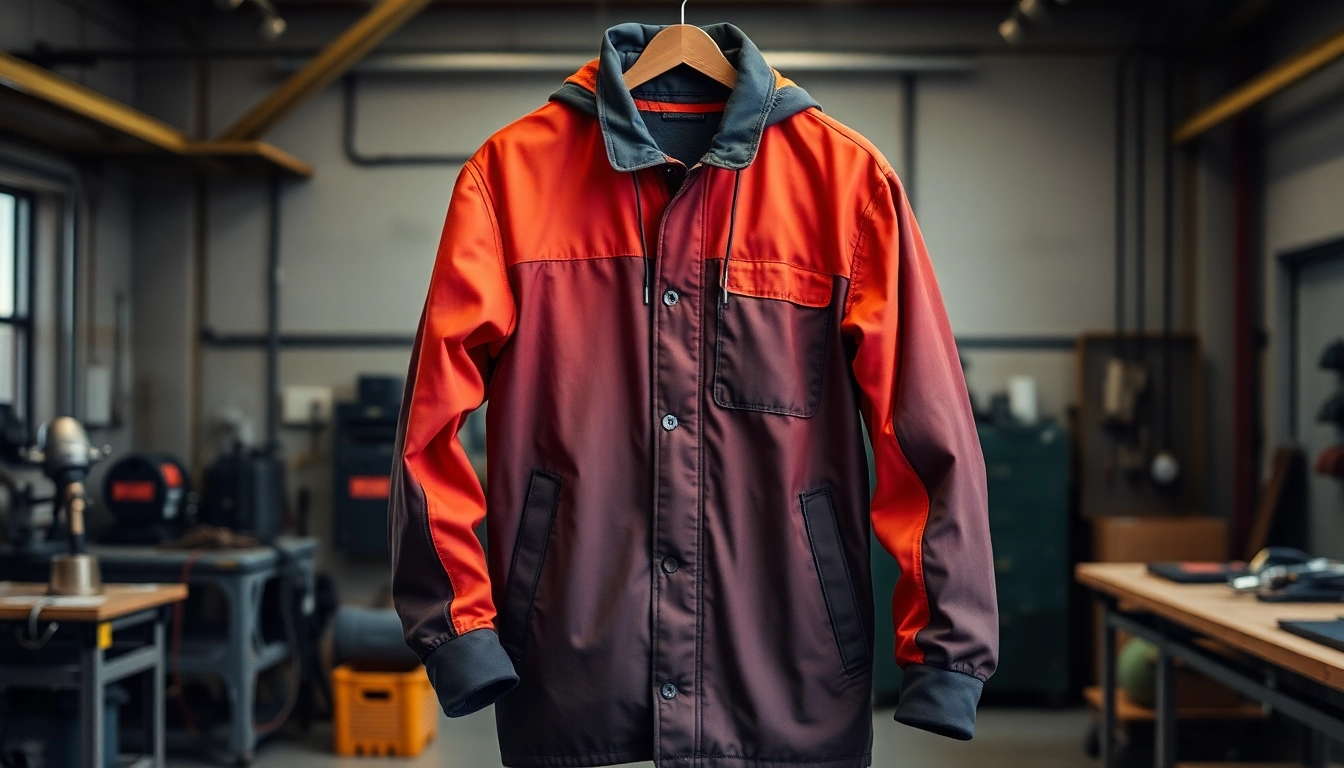
Understanding Welding Jackets: Benefits and Features
Welding jackets are essential pieces of protective clothing designed for individuals who work with welding tools and processes. These jackets offer a critical layer of protection against hazards such as sparks, heat, and harmful substances that are prevalent in welding environments. A well-chosen welding jacket not only ensures safety but enhances comfort and mobility, allowing welders to perform tasks efficiently.
What Makes a Welding Jacket Flame Resistant?
Flame resistance is a crucial feature of welding jackets. This property comes from the materials used in their construction, which are often treated with flame-retardant chemicals or inherently flame-resistant fibers. When welding, the intense heat generated can ignite ordinary fabrics, leading to serious injuries. Flame-resistant materials have been engineered to prevent ignition and limit the spread of flames, providing added security for welders.
Additionally, flame-resistant jackets are designed to withstand high temperatures and resist melting. The most common materials include treated cotton, leather, and specialized synthetic fibers, which provide multiple layers of safety and comfort. For example, jackets made from leather are particularly effective because they can withstand higher temperatures and thermal impacts compared to traditional cotton.
Material Types Used in Welding Jackets
There are several materials commonly used in the construction of welding jackets, each offering unique benefits:
- Cotton: Treated cotton is lightweight and breathable, making it suitable for warmer environments. Its natural fiber allows for ventilation, which helps prevent overheating during welding tasks.
- Leather: Leather welding jackets provide superior durability and heat resistance. They are resistant to abrasion and punctures, ideal for heavy-duty applications. However, leather can be heavier and less breathable than cotton.
- Synthetic Materials: Fabrics like Nomex and Kevlar are engineered for flame resistance and are often more lightweight than leather, providing good flexibility while ensuring high levels of protection. These materials also maintain their properties through repeated washes.
Key Features to Look for in a Welding Jacket
When selecting a welding jacket, consider the following features to ensure optimum protection and comfort:
- Flame Resistance: Look for jackets certified as flame-resistant according to industry standards. Ensure they meet or exceed ANSI/ISEA standards for protective apparel.
- Size and Fit: A good fit is critical for safety and mobility. Jackets should allow for a full range of motion while being fitted but not overly tight. Adjustable cuffs and waistbands can enhance personalized comfort.
- Pockets: Functionality is also important; jackets with several pockets can provide convenient storage for tools and welding accessories.
- Ventilation: To improve breathability and comfort, jackets with vents or mesh lining can prevent overheating in warmer environments.
- Reinforced Areas: Look for reinforced seams and areas where wear and tear might occur, such as the shoulders and elbows, which will extend the life of the jacket.
Choosing the Right Welding Jacket for Your Needs
Choosing the right welding jacket is essential for ensuring safety and achieving optimal performance in diverse welding environments. Consider the following aspects before making a purchase.
Finding the Perfect Fit for Comfort and Safety
Fit can affect both safety and comfort levels. A welding jacket that is too loose may snag on equipment, posing a safety risk, while a jacket that is too tight can restrict movement and lead to fatigue. Ensure that the sleeves are long enough to cover the wrists when arms are extended and that the body length is sufficient to cover the waist, especially during bending or squatting actions. Many brands provide size charts to assist buyers in selecting the correct size based on their measurements.
Recommended Welding Jacket Styles for Different Applications
The style of the jacket can vary based on the specific type of welding and individual preferences. Here are some recommended styles:
- Traditional Jacket: Ideal for most welding applications, featuring long sleeves and a high collar to protect the neck.
- Hooded Welding Jacket: Offers additional protection to the head and neck, suitable for outdoor welding tasks or environments where sparks may be prevalent.
- Lightweight Welding Jacket: Best for MIG and TIG welding where heat is less intense, these jackets may offer less bulk and more comfort for intricate work.
How to Determine the Right Material for Your Working Environment
Consider the specific environment in which welding will take place. For example, if you’re welding in a confined space or during the summer months, a lightweight, breathable cotton jacket may be more suitable. Conversely, if you’re working in high-heat conditions or outdoors, a leather jacket may offer superior protection against temperature and environmental hazards.
Understanding the ISO classification for flame-resistance ratings will aid in making an informed decision on material choice. Always review the working conditions and adjust the jacket style and material accordingly.
Maintenance and Care for Welding Jackets
Proper maintenance of welding jackets is essential to ensure they remain effective in protecting against hazards. Follow these tips for cleaning and care to prolong the life of your jacket.
Cleaning Techniques for Different Jacket Materials
Cleaning methods will vary by material. For cotton jackets, spot cleaning often suffices. When washing, use cold water and a mild detergent to prevent damaging the flame-retardant properties of the fabric. Avoid using bleach or fabric softeners that may weaken materials.
Leather jackets should not be cleaned with water. Instead, use a leather cleaner and conditioner to maintain suppleness while protecting against damage. Ensure you follow manufacturer guidelines for best results.
For synthetic jackets, check the care instructions. Most can be machine washed on a gentle cycle, but always air-dry to prevent shrinking.
How to Store Your Welding Jacket Properly
When not in use, store your welding jacket in a cool, dry place away from direct sunlight, which can degrade materials over time. Hanging the jacket on a sturdy hanger can prevent wrinkling and maintain its shape.
Avoid folding jackets in a way that could create creases. If space is limited, consider vacuum-sealable bags to minimize space while keeping the jacket clean and protected.
Signs It’s Time to Replace Your Welding Jacket
Even the best welding jackets have a lifespan. Here are signs that your jacket may need replacing:
- Visible Wear and Tear: Look for fraying seams, holes, or significant discoloration that may indicate damage to the fabric’s flame-resistant properties.
- Loss of Fit: If the jacket has stretched out significantly, it may no longer provide adequate protection.
- Persistent Odor: If a cleaning can’t remove the smell of smoke or burnt material, it’s sensible to replace the jacket to ensure safety and hygiene.
Exploring Popular Brands and Models of Welding Jackets
The market is full of reputable brands offering a variety of welding jackets. Familiarity with these brands can assist in selecting quality options tailored to specific needs.
Top Brands to Consider for Quality Welding Jackets
Consider these well-rated brands known for their craftsmanship and protective features in welding jackets:
- Lincoln Electric: Offers a wide range of jackets, including options specifically designed for women and made from high-quality materials.
- Miller Electric: Known for innovative designs and durability, their jackets are favored by professionals in various welding applications.
- Black Stallion: This brand manufactures a selection of rugged jackets that combine leather, cotton, and synthetic materials aimed at heavy-duty protection.
- Revco: Provides stylish and functional welding jackets that are flame resistant and cater to a variety of working conditions.
Comparing Prices for Welding Jackets: What to Expect
Welding jacket prices can greatly vary based on brand, material, and specific features. Here are some general price ranges you can expect:
- Budget Options: $20 – $50 for basic, lightweight cotton jackets.
- Mid-Range Options: $50 – $150 for durable cotton or blended jackets with enhanced features.
- High-End Options: $150 and above for specialized leather jackets or those with advanced protective technologies.
User Reviews and Ratings of Leading Welding Jackets
Reading user reviews and ratings can provide insights into the practical performance and durability of specific jackets. Pay attention to feedback regarding comfort, fit, and how well the jacket holds up after multiple washing cycles. Ratings often reflect buyer satisfaction and can guide future purchases.
Safety Standards and Regulations for Welding Jackets
Welding safety gear must comply with established standards to ensure adequate protection in various environments. Familiarizing yourself with these regulations can help in making informed choices about protective clothing.
Understanding NFPA and ANSI Standards for Protective Apparel
The National Fire Protection Association (NFPA) and the American National Standards Institute (ANSI) set forth guidelines for protective garments in welding:
- NFPA 701: This standard addresses the flammability of fabrics and materials, establishing criteria that welding gear must meet.
- ANSI/ISEA 105: This standard provides test methods and performance ratings for protective clothing in relation to hazards such as heat and flame.
When shopping for a welding jacket, ensure it meets these critical standards to offer reliable protection in active work environments.
The Importance of Compliance in Welding Safety Gear
Compliance with established safety standards is crucial to minimizing workplace injuries. Using jackets that meet or exceed industry standards protects against hazardous conditions, reduces the risk of burns, and prevents accidents that can arise from insufficient protection.
Employers should ensure that their team is equipped with suitable PPE (Personal Protective Equipment) and that these items are regularly inspected to maintain compliance and safety while welding.
How Welding Jackets Enhance Workplace Safety Culture
Implementing a standard protocol that includes mandatory use of welding jackets enhances safety awareness in the workplace. Training sessions that emphasize the importance of proper protective gear help establish a culture of safety, reducing the likelihood of mishaps during welding tasks.
Employers can also foster continuous improvement by engaging employees in discussions about safety practices and modifying policies based on collective feedback to better serve the welding team.