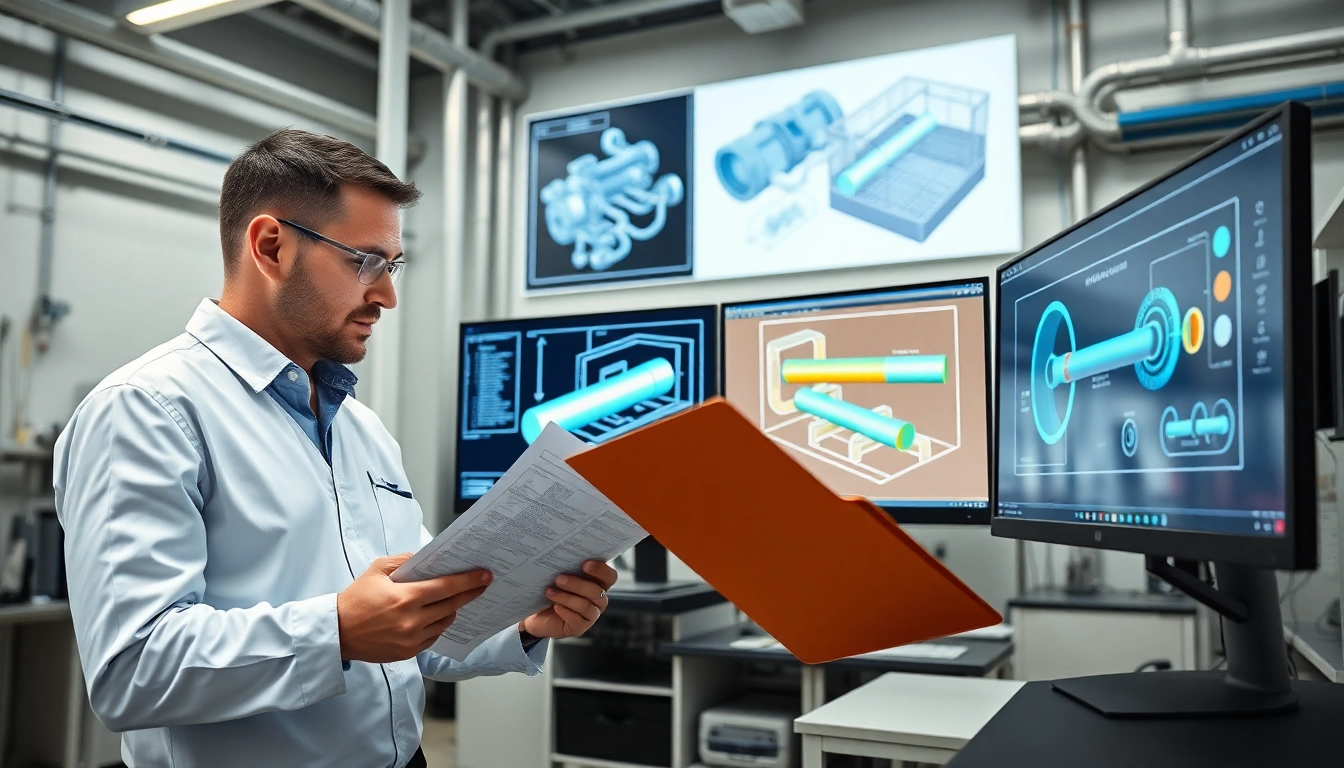
Understanding Piping Stress Analysis
What is Piping Stress Analysis?
Piping Stress Analysis is a critical engineering process that evaluates the stresses and strains within piping systems under various conditions. By analyzing these stresses, engineers can ensure that piping systems operate safely and efficiently without compromising performance. The analysis takes into account various factors, including loads, temperature changes, and material properties. The primary goal is to identify any potential risks of failure, allowing for design modifications or reinforcements to be implemented before issues arise.
Importance in Engineering
The significance of piping stress analysis company cannot be overstated in the engineering sector. Every piping system is susceptible to mechanical failure due to the environmental and operational conditions it endures. Stress analysis helps in demonstrating compliance with regulatory standards and codes, providing assurance that systems can handle operational stresses and thermal expansion without risk of rupture or joint failure. Moreover, proactive stress analysis leads to increased efficiency and minimized operational costs by reducing the need for maintenance and preventing unexpected downtime due to pipe failures.
Key Terminologies Explained
- Static Load: This refers to the weight of the piping itself, along with any additional weight from the fluid it transports.
- Dynamic Load: These are loads that result from movement, such as vibrations, fluid movement, and seismic activity.
- Thermal Expansion: This is the tendency of materials to expand when heated and contract when cooled.
- Stress: This refers to the internal resistance offered by the material against external forces applied to it.
- Strain: A measure of deformation representing the displacement between particles in a material body.
Core Principles of Stress Analysis
Static and Dynamic Loads
Understanding loads is fundamental to effective piping stress analysis. Static loads are relatively constant and predictable, such as the weight of the pipe itself and the fluid it contains. These loads can be calculated using the density of the materials involved and their geometric configurations.
Dynamic loads, on the other hand, introduce complexities due to their time-dependent nature. Examples include pressure surges, vibrations from pumps and other machinery, or environmental forces like wind and earthquakes. Piping systems must be designed to accommodate these variations without exceeding material limits.
Thermal Expansion Effects
As temperature changes, materials will expand or contract, affecting the stress levels experienced within a piping system. It is critical to analyze thermal expansion accurately, especially in environments with extreme temperature variations. Engineers typically apply expansion loops, bends, or flexibility strategies to accommodate these changes and mitigate stresses caused by thermal effects.
Material Selection Considerations
The materials selected for a piping system can significantly impact its integrity and life span. Engineers must consider factors such as corrosion resistance, strength, flexibility, and temperature resilience when choosing materials. Common materials in piping systems include steel, copper, and various types of plastics. Each material has distinct advantages and disadvantages, thus requiring careful evaluation based on the specific operational context of the piping system.
Challenges in Piping Stress Analysis
Common Issues Faced
Piping stress analysis can be fraught with challenges. One of the most considerable hurdles is accurately capturing the real-world behavior of piping systems. Assumptions made during modeling may not reflect how systems perform in actual conditions, leading to unreliable results. Other issues arise from the complexity of integrating various loads, thermal effects, and material properties into a cohesive analysis.
Overcoming Technical Barriers
To effectively overcome these challenges, it is essential to employ state-of-the-art simulation tools and software, along with guidelines for best practices in stress analysis. Continual training and awareness of the latest codes and standards in the industry are also vital. Implementing peer reviews during the design phase can help catch potential inconsistencies and provide multiple perspectives on the analysis.
Real-World Case Studies
Consider a scenario where a chemical processing plant experienced recurrent pipe failures due to unaccounted dynamic loads in their stress analysis. Post-failure analysis indicated that the initial stress calculations were flawed due to not considering the machinery-induced vibrations adequately. By employing more advanced modeling software that included dynamic load simulations, the engineering team redesigned the piping with flexibility in mind, significantly reducing failure rates.
Best Practices for Conducting Stress Analysis
Guidelines for Effective Analysis
Effective piping stress analysis requires adherence to best practices. It is recommended to start with a thorough understanding of the entire system layout and conditions it faces. Collaborating with multi-disciplinary teams during the design process can yield more accurate models, and regular updates to analysis protocols based on industry advancements can enhance reliability. Documentation of assumptions and calculations is equally important to maintain transparency throughout the process.
Tools and Software Recommendations
Several tools and software are instrumental in conducting piping stress analysis. Well-known options include CAEPIPE, AutoPIPE, and ANSYS. These software applications offer user-friendly interfaces and robust simulation capabilities, allowing for the assessment of various load conditions and thermal influences on the piping systems. It is crucial to choose tools that align with project specifications and industry standards.
Quality Assurance Measures
Implementing a strong quality assurance process can mitigate risks associated with piping stress analysis. This involves establishing a methodical approach to verifying results via cross-checks against established codes and standards, as well as performing sensitivity analysis to see how variations in input parameters might impact outcomes. Regular audits of engineering processes can further enhance the reliability of stress analysis results.
The Future of Piping Stress Analysis
Emerging Technologies
As technology continues to evolve, innovative tools such as artificial intelligence (AI) and machine learning (ML) are being integrated into piping stress analysis. These technologies can significantly improve predictive capabilities, allowing engineers to foresee potential failures before they happen. The implementation of IoT devices also allows for real-time monitoring of piping systems, providing data that can inform ongoing analysis and maintenance decisions.
Integrating Sustainable Practices
In the face of increasing environmental concerns, incorporating sustainable practices into piping systems is becoming paramount. Strategies such as using recyclable materials and optimizing system designs to reduce energy consumption are gaining traction. Stress analysis plays a vital role here by helping to identify areas where sustainability enhancements can be made without sacrificing system integrity or performance.
The Role of Innovations in Engineering
The engineering landscape is rapidly changing with advancements in technology and methods, requiring a proactive approach to stress analysis. New materials, modeling techniques, and construction practices are redefining how piping systems are analyzed and built. Embracing these innovations is crucial for engineering firms aiming to stay competitive, as they can offer enhanced capabilities, improve safety, and reduce costs.