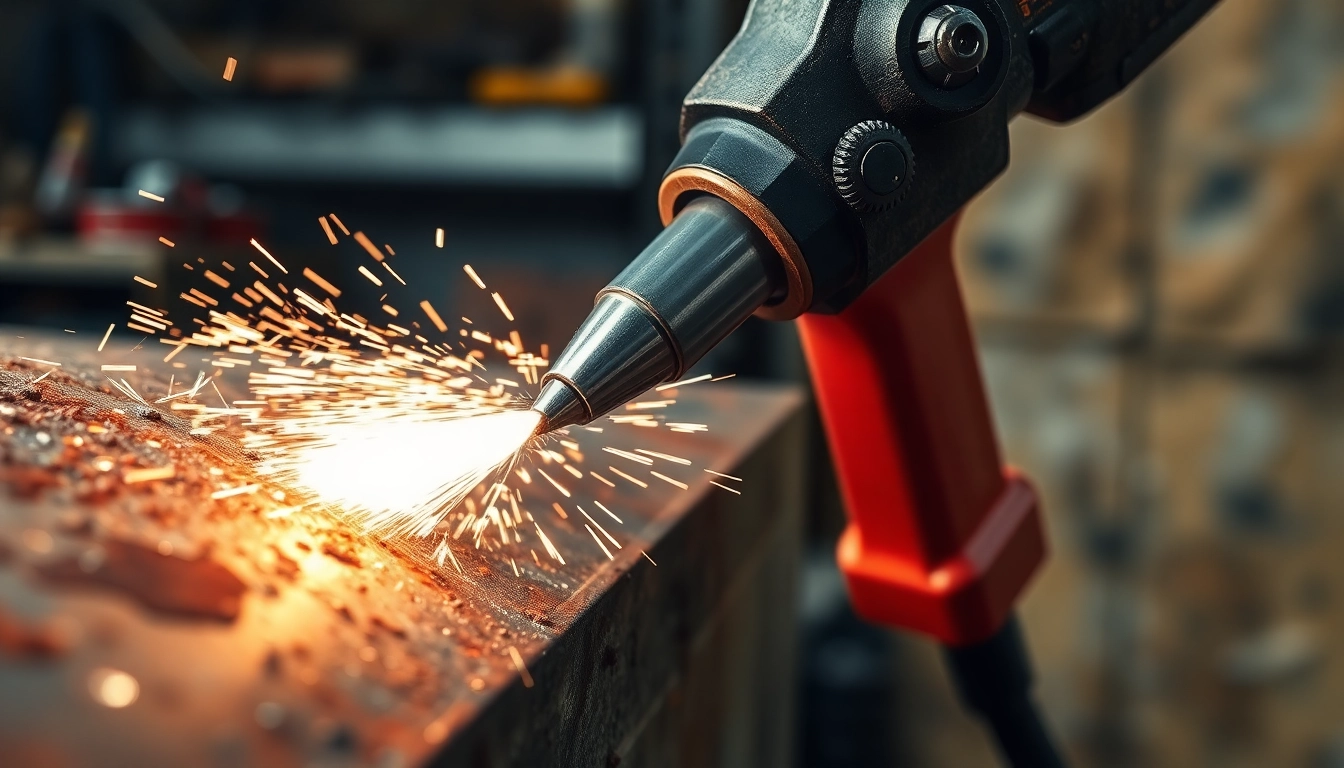
Introduction to Needle Guns and Their Applications
Needle guns, also known as needle scalers, are powerful tools widely used for surface preparation in various industries. These tools utilize a rapid hammering action to remove unwanted materials such as rust, paint, and mill scale from metal surfaces. Their significance in industrial applications cannot be overstated; they provide efficient and effective surface treatment, paving the way for further processes like welding and painting. In this article, we will delve into the mechanics, applications, and innovations associated with needle guns, ensuring you grasp their role in modern workmanship and maintenance.
What is a Needle Gun?
A needle gun is primarily a pneumatically-operated hand tool designed to clean surfaces by using a series of steel needles that vibrate rapidly, creating a powerful impact on the surface material. The key mechanism behind its operation is the use of compressed air, which drives the needles back and forth with significant force. Unlike traditional tools used for scraping or sanding, needle guns are particularly adept at reaching into seams and crevices, where other tools might struggle.
Needle guns vary in design, with some resembling pistol grips while others have straight configurations. The choice of design often depends on the specific application and user preference. Regardless of the style, the core functionality remains focused on enhancing surface conditions for subsequent treatments.
Common Uses in Various Industries
Needle guns find applications across numerous sectors, including:
- Construction: They are invaluable in preparing surfaces for painting and coating, ensuring that all contaminants are effectively removed.
- Aerospace: In this sector, they are used for meticulous surface preparation around precision-engineered components.
- Automotive: Mechanics often employ needle guns to clean old paint and rust from parts to ensure a proper bond during repainting.
- Marine: Shipyards utilize needle guns for maintaining the integrity of metal surfaces subjected to harsh marine environments.
- Manufacturing: Many factories use needle guns to prepare surfaces for welding, ensuring that joints are clean and free from contaminants.
Key Benefits of Using a Needle Gun
The advantages of needle guns are numerous:
- Efficiency: The rapid action of the needles allows for quick removal of materials, drastically reducing preparation time.
- Versatility: They can effectively work on various surfaces, including irregular shapes and hard-to-reach areas.
- Operator Comfort: Modern needle guns are designed for ease of use, with ergonomic grips minimizing user fatigue during prolonged operation.
- Environmental Impact: Using a needle gun usually reduces the need for chemical solvents, leading to a more eco-friendly workspace.
How Needle Guns Work: Mechanism and Technology
Understanding the Components of a Needle Gun
To appreciate the functionality of needle guns, it’s essential to understand their core components:
- Needle Assembly: Composed of several spring-loaded needles, this assembly is the primary mechanism that delivers the cleaning action.
- Motor or Air Supply: For pneumatic needle guns, a reliable air compressor is required. Electric models often include a built-in motor.
- Trigger Mechanism: This allows operators to control the activation and deactivation of the tool, enhancing safety and precision during application.
- Housing: The housing encases the inner components while providing a comfortable grip and balance during use.
Types of Needle Guns: Electric vs Pneumatic
Needle guns come in two primary forms: pneumatic and electric.
- Pneumatic Needle Guns: These are operated using compressed air and are known for their robustness and power, making them ideal for heavy-duty tasks. Their use in industrial applications is prevalent, particularly due to their high impact rates and overall efficiency.
- Electric Needle Guns: These models are powered by electricity and tend to be more portable due to the absence of air hoses. While they may not match the power of pneumatic models, electric needle guns are perfect for lighter tasks and are user-friendly, especially in smaller workshops.
Maintenance Tips for Optimal Performance
Ensuring that your needle gun operates at peak performance involves regular maintenance:
- Regular Cleaning: After use, it’s crucial to wipe the needle assembly and remove debris that may accumulate. This prevents clogging and maintains effectiveness.
- Check for Wear: Inspect the needles frequently for signs of wear. Replace them if they become dull to maintain performance efficiency.
- Lubrication: Apply lubricant to the moving parts according to the manufacturer’s instructions to reduce friction and prolong the tool’s lifespan.
- Inspect Air Supply: For pneumatic models, ensure your air compressor provides adequate pressure and check for any leaks in the hose.
Step-by-Step Guide to Using a Needle Gun
Preparation for Surface Treatment
Preparing the workspace is critical for effective use of a needle gun:
- Workspace Cleanup: Remove any loose materials and debris around the work area to prevent them from interfering with the cleaning process.
- Personal Protective Equipment (PPE): Always wear appropriate PPE, including gloves, goggles, and a dust mask, to protect against flying debris and dust.
- Setting Up Tools: Ensure that all necessary tools, including the needle gun, air compressor (if applicable), and work surfaces, are ready and accessible.
Operating the Needle Gun Safely
Operating a needle gun requires adherence to safety protocols:
- Read the Manual: Familiarize yourself with the specific operating instructions provided by the manufacturer.
- Proper Grip: Always hold the needle gun securely, using both hands if possible, to maintain control during use.
- Avoid Contact with Skin: Keep the tool at a safe distance from your body to avoid accidental injuries.
- Work in a Ventilated Area: Ensure proper ventilation to reduce the inhalation of debris and dust while operating the needle gun.
Best Practices for Effective Results
To achieve the best results when using a needle gun, consider the following best practices:
- Test on a Small Area: Before tackling larger projects, test the needle gun on a small section to gauge its effectiveness and adjust pressure settings as necessary.
- Maintain Consistent Motion: Move the needle gun in a consistent pattern across the surface to avoid uneven cleaning.
- Monitor Performance: Watch the condition of the needles during use and be prepared to replace them if performance noticeably declines.
- Finish with Additional Tools: After completing the initial cleaning with the needle gun, consider using sanders or blasting tools for finer finishing.
Troubleshooting Common Issues with Needle Guns
Identifying Performance Problems
Even the best tools can face performance issues. Common problems to look for include:
- Poor Cleaning Performance: This may indicate dull needles, insufficient air pressure for pneumatic models, or improper technique.
- Excessive Vibration: Excessive vibration can cause user discomfort and can indicate mechanical issues within the gun.
- Needle Breakage: Frequent needle breakage can result from improper usage or worn-out needles that need replacing.
Solutions for Common Malfunctions
If you encounter performance issues, consider the following solutions:
- Replace Needles: Keep spare needles and replace dull or broken ones promptly to maintain optimal performance.
- Adjust Air Pressure: For pneumatic units, ensure the air supply meets the required pressure specs outlined by the manufacturer.
- Regular Maintenance: Adhere to regular maintenance schedules to enhance performance and prolong the tool’s lifespan.
When to Seek Professional Help
If problems persist after attempting troubleshooting, consider seeking professional assistance
Consulting a technician is advisable if:
- The tool exhibits unpredictable behavior or severe vibration.
- You lack confidence in performing repairs or maintenance.
- There are visible signs of wear in internal components or the motor that might require specialized knowledge for repair.
Future Trends in Needle Gun Technology
Innovations in Design and Functionality
As technology continues to evolve, needle guns are also likely to experience significant advancements:
- Smart Technology: Integrating smart technology to monitor performance and diagnose issues could become a common feature, improving efficiency and user experience.
- Enhanced Ergonomics: Future designs may focus on even more comfortable handling, reducing user fatigue and increasing productivity during prolonged usage.
- Battery-Powered Options: With the growing demand for battery-powered tools, manufacturers may innovate compact and powerful cordless needle guns.
Environmental Considerations in Tool Development
Environmental sustainability is a growing concern across industries. Future needle guns may be designed with eco-friendly materials and energy-efficient options, emphasizing reduced waste and energy consumption. Additionally, enhancing the recyclability of components will be critical in addressing environmental impacts.
Predictions for Market Growth and User Adoption
The needle gun market is expected to grow as industries continue to emphasize surface preparation and maintenance. As more professionals recognize the efficiency and effectiveness of needle guns, adoption rates are likely to increase. Coupled with advancements in technology and design, it is anticipated that these tools will become even more integral to various industries focused on metalwork and surface treatment.