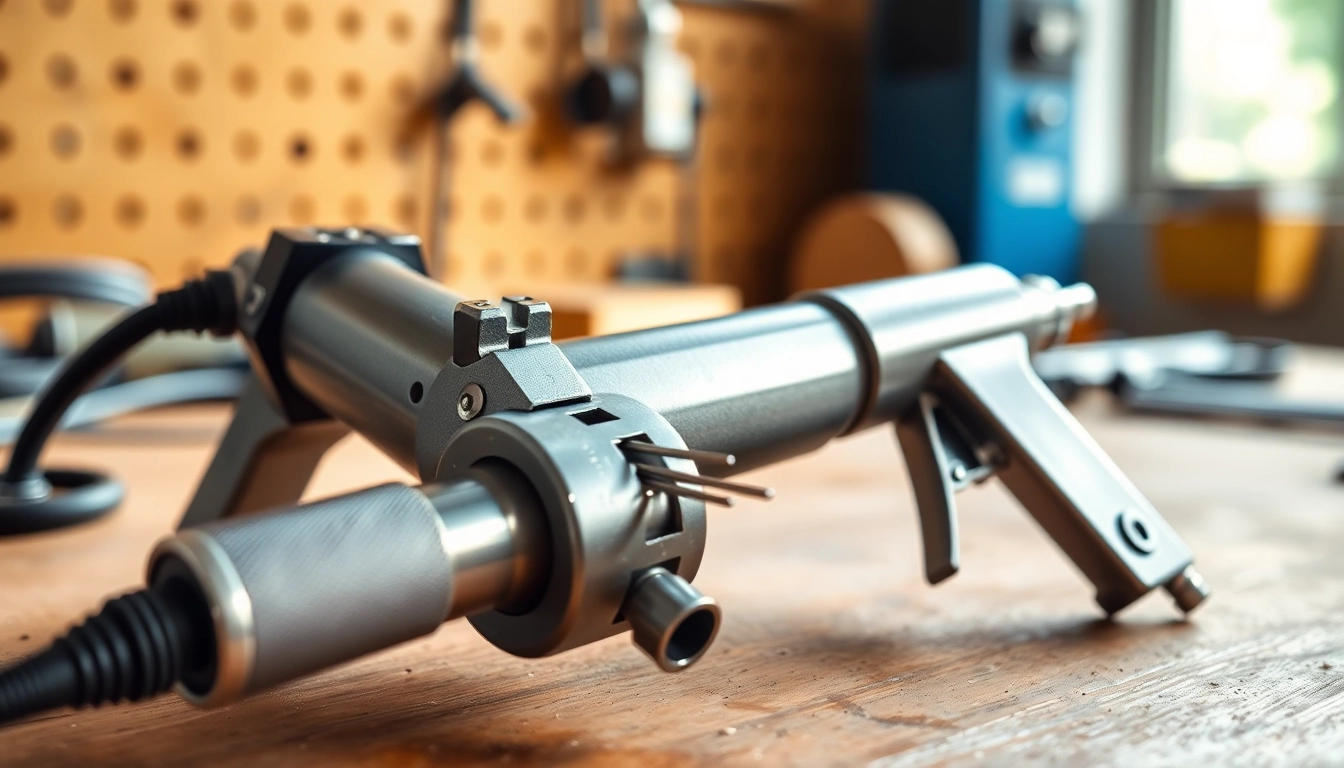
Introduction to Needle Guns
Needle guns, commonly referred to as needle scalers, are powerful tools designed for surface preparation and material removal in various industries, including automotive, construction, and metalworking. These tools utilize high-speed, pneumatic or electric mechanisms to vibrate thin steel needles, efficiently removing rust, scale, old paint, and contaminants from metal surfaces. Among the many options available in the market, the needle gun by Von Arx stands out for its efficiency and user-friendly design. In this article, we will explore the intricacies of needle guns, how they work, safety measures, maintenance, and techniques for maximizing their effectiveness, ensuring you get the most out of your investments.
What is a Needle Gun?
A needle gun, or needlegun scaler, is a specialized tool meant to remove unwanted materials from metal surfaces. It accomplishes this through rapid, high-frequency vibrations created by air pressure or electrical power, dislodging rust and paint without damaging the underlying metal. They come in various configurations, mainly pneumatic or electric, serving distinct operational needs in different environments. This versatile tool has its roots in the industrial world but has gained popularity among DIY enthusiasts and tradespeople for home and automotive projects.
Different Types of Needle Guns
Needle guns can generally be categorized based on their power source and design, impacting their application and performance:
- Pneumatic Needle Guns: These tools rely on compressed air to function. They are particularly effective for heavy-duty applications, providing more power and speed, which makes them ideal for large-scale jobs involving extensive rust and paint removal.
- Electric Needle Guns: Powered by electricity, these models are often lighter and more portable, making them suitable for smaller projects or in settings where access to compressed air is limited. They tend to be quieter and easier to handle, ideal for home repairs or light automotive work.
- Combination Models: Some needle guns integrate pneumatic and electric features, allowing users to switch between power sources depending on the task’s demands.
Common Uses for Needle Guns
Needle guns are prominently utilized in various tasks, such as:
- Surface Preparation: Before applying coatings, it is essential to clean surfaces thoroughly. Needle guns excel at removing coatings such as paint, varnish, and rust, ensuring a smooth application.
- Metal Restoration: These tools play a significant role in restoring old metal surfaces by removing layers of rust and grime, extending the life of items such as machinery and vehicles.
- Industrial Applications: In manufacturing and repair sectors, needle guns are used for maintaining machinery and industrial equipment, providing necessary surface cleaning to prevent wear and corrosion.
- Shipbuilding and Maintenance: The maritime industry extensively uses needle guns for ship hull cleaning, where the removal of marine growth and rust is critical for maintenance and safety.
How Needle Guns Work
The Mechanics of Needle Guns
Understanding the working mechanics of a needle gun is vital for its effective usage. At the heart of the needle gun is a series of long, thin needles housed within a single or multiple nozzle setups. When activated, whether pneumatically or electrically, these needles vibrate rapidly.
The vibrations are generated through different mechanisms depending on the type of needle gun:
- Pneumatic Models: In pneumatic needle guns, compressed air enters the gun and drives a hammer mechanism that creates the rapid motion of the needles. This method allows for high strokes per minute, making it particularly effective for tough materials.
- Electric Models: Electric needle guns convert electrical energy into mechanical vibrations using a motor, oscillating the needles at high speeds to dislodge unwanted materials.
The result is a powerful action that makes these tools incredibly efficient for surface cleaning and preparation.
Understanding Needle Gun Specifications
Choosing the right needle gun involves understanding various specifications that differentiate models. Some primary considerations include:
- Needle Count: Most models include a set of several needles, ranging typically from 4 to 19. A higher needle count generally provides faster results as more surface area can be treated simultaneously.
- Strokes Per Minute (SPM): This measures how often the needle vibrates in a minute. Higher SPM indicates faster material removal, crucial for heavier jobs.
- CFM Requirements: For pneumatic models, understanding the Cubic Feet per Minute (CFM) requirement is essential, as it determines the air compressor’s size needed for optimal operation. Typical requirements range from 6 CFM to upwards of 16 CFM at 90 PSI.
- Weight and Ergonomics: The weight of the needle gun may affect usability, especially during extended use. Lightweight and ergonomically designed models help reduce fatigue and increase productivity.
Choosing the Right Needle Gun for Your Needs
Selecting the appropriate needle gun requires matching the tool to your specific needs. Factors include:
- Project Size: For industrial-scale tasks, a heavy-duty pneumatic model may be ideal, while smaller projects can benefit from lightweight electric options.
- Material Being Treated: If you’re working with significantly rusted surfaces, opt for models with a higher needle count and SPM ratings.
- Accessibility: For jobs in confined spaces, a more compact model can provide better maneuverability.
Safety Measures with Needle Guns
Personal Protective Equipment (PPE)
Safety is paramount when using needle guns, as they produce high-velocity impacts that can pose risks. Essential PPE includes:
- Safety Glasses: Protect your eyes from debris and particles that can become airborne during operation.
- Hearing Protection: High noise levels produced by needle guns necessitate the use of ear protection to prevent hearing loss.
- Respiratory Protection: Depending on the material being removed (like old paint or coatings), wearing a respirator can protect your lungs from harmful fumes and dust.
- Gloves: Durable work gloves shield your hands from vibration and provide a secure grip.
Safe Operating Procedures
To ensure safe operation of needle guns, follow these guidelines:
- Inspect Before Use: Always inspect the tool for any wear or damage before operating. Ensure needles are securely attached.
- Work in a Well-Ventilated Area: Ensure proper airflow to avoid inhaling harmful dust or vapors.
- Secure Workpieces: Ensure that materials being cleaned are secured to prevent movement during operation.
- Follow Manufacturer Instructions: Adhere to the specific operational guidelines outlined in the user manual for your needle gun model.
Common Risks and How to Avoid Them
Understanding the common risks associated with needle gun operation is vital for preventing accidents:
- Physical Injuries: Injuries can result from flying debris. Always wear appropriate protective gear.
- Noise-Induced Hearing Loss: Prolonged exposure to high noise levels can damage hearing. Equip yourself with noise-canceling headphones.
- Dust Inhalation: Inhalation of hazardous dust can lead to respiratory issues. Use appropriate respiratory protection, and work in a ventilated space.
Maintenance and Care for Needle Guns
Regular Maintenance Checks
Regular maintenance is essential for the longevity and efficiency of needle guns. Key maintenance practices include:
- Cleaning: After each use, clean the needle gun to remove debris, dust, and residues that could impair its functionality.
- Needle Inspection: Regularly inspect needles for wear and tear; replacing them promptly will ensure optimal performance and prevent damage to surfaces.
- Lubrication: For pneumatic models, ensure adequate lubrication on moving parts to maintain smooth operation.
Cleaning and Storage Best Practices
Proper cleaning and storage of needle guns can extend their lifespan significantly:
- Post-Use Cleaning: Wipe down the exterior of the needle gun and clean the needle area to prevent clogging.
- Dry Storage: Store the tool in a dry place to avoid rusting and damage due to moisture.
- Organize Parts: Keep all parts organized and accessible. Proper organization prevents loss and ensures quick assembly and operation.
Troubleshooting Common Issues
Even with regular upkeep, users may encounter issues. Here are some common problems and their solutions:
- Needles Not Vibrating: Check for air supply issues in pneumatic models or electrical connection problems in electric models.
- Poor Performance: Ensure that the tool is clean and that the needles are not worn out; replace them if necessary.
- Excessive Noise: If the needle gun operates louder than usual, it may require lubrication or service to tighten any loose parts.
Maximizing Efficiency with Needle Guns
Best Techniques for Surface Preparation
Achieving the best results with needle guns involves employing various techniques to maximize efficiency:
- Correct Angle and Pressure: Hold the needle gun at an appropriate angle against the surface, applying consistent pressure for even material removal.
- Work in Sections: Tackling one section at a time helps manage workflow and ensures thorough coverage without missing spots.
- Utilize Multiple Needles: If your model allows, employ multiple needles for large areas to speed up the process.
Integrating Needle Guns into Your Workflow
To seamlessly incorporate needle guns into regular operations, consider the following:
- Assess Compatibility: Evaluate existing tools to ensure compatibility with needle guns for a well-rounded toolkit.
- Training Personnel: Properly train personnel in the operation, maintenance, and safety protocols of needle guns to enhance overall productivity.
- Feedback for Improvements: Regularly seek feedback from users about ease of use and performance to identify potential upgrades or adjustments to your workflow.
Performance Metrics and Improvement Strategies
Establishing performance metrics can help gauge the efficiency of needle guns:
- Time to Completion: Measure the time taken to complete surface preparation tasks to identify areas for improvement.
- Quality of Finish: Evaluate the quality of surfaces post-treatment to ensure a high standard before subsequent applications such as painting or sealing.
- Cost Analysis: Assess the cost-effectiveness of needle gun operation versus alternative methods to justify investment in quality models.
Conclusion
In conclusion, needle guns are invaluable tools for efficient surface preparation and remediation tasks across various industries. Understanding their mechanisms, appropriate usage, safety measures, and maintenance practices are crucial for maximizing their performance. By integrating these tools effectively in your workflow, you can achieve optimal results, ensuring that both time and resources are utilized efficiently. With proper care and techniques, your needle gun can be a long-lasting investment that aids in maintaining the integrity and aesthetics of metal surfaces.