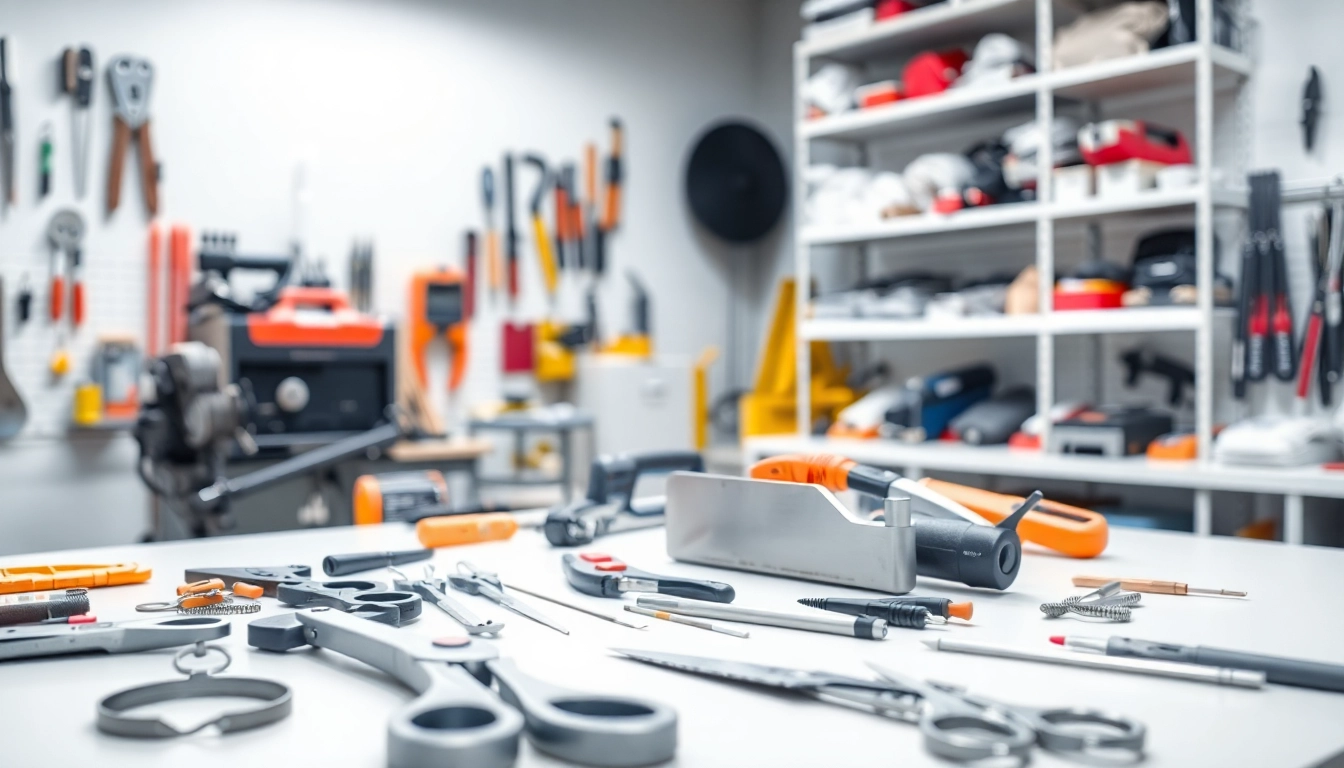
Understanding Cutting Equipment: Types and Uses
1. Overview of Cutting Equipment
Cutting equipment plays a pivotal role in various fields, from manufacturing and construction to culinary arts and crafting. These tools are designed for precisely dividing materials into desired shapes and sizes, and their selection depends heavily on the specific needs of a project and the kind of material being processed. The evolution of cutting tools from simple hand-operated devices to sophisticated machines has transformed efficiency and precision in productivity. Whether you’re looking for industrial-grade machines or basic tools for home projects, cutting equipment encompasses a wide range of devices designed for different applications.
2. Common Types of Cutting Equipment
Cutting equipment can be categorized based on their design, function, and the materials they are used to cut. Here are some prevalent types:
- Knives and Blades: Essential in kitchens and workshops, these hand-held tools include chef knives, utility knives, and various types of blades specifically designed for different cutting tasks.
- Saws: This category includes hand saws, band saws, circular saws, and jigsaws that are utilized for cutting wood, metal, and other materials efficiently.
- Scissors and Shears: Commonly found in both office and home environments, these tools are used for cutting paper, fabric, and other lightweight materials.
- Laser Cutters: These advanced machines use laser technology to create precise cuts on various materials, including metals, plastics, and wood, often employed in manufacturing and prototyping.
- Water Jet Cutters: Utilizing high-pressure water jets, these machines are capable of cutting through tough materials like stone and metal without introducing heat that can change the material’s properties.
- Plasma Cutters: These devices generate a plasma arc to melt metal and are commonly used in industrial applications for cutting thick metals.
3. Equipment Uses Across Different Industries
Cutting equipment serves a multitude of purposes across various industries:
Manufacturing
Precision is crucial in manufacturing, where cutting equipment such as CNC machines and laser cutters are used for producing components that meet stringent specifications. These tools reduce waste and increase efficiency while maintaining safety and precision.
Culinary Arts
In the kitchen, various knives and blades are essential for food preparation. From slicing and dicing to intricate designs in culinary presentations, the right cutting tools can enhance a chef’s creativity and efficiency.
Construction
Cutting equipment such as circular saws, concrete saws, and shears are fundamental in construction, helping professionals to cut materials like wood, drywall, and metal sheets accurately.
Crafting and DIY Projects
Hand tools, including scissors and hobby knives, are staples for crafters. High-precision cutting machines, like those offered by Cricut, allow for intricate designs that are essential for a variety of crafts, from scrapbooking to clothing design.
Choosing the Right Cutting Equipment for Your Needs
1. Assessing Your Project Requirements
Before selecting cutting equipment, it’s essential to assess the specific requirements of your project. Understanding the materials involved, the scale of the project, and the desired precision will guide your choice:
- Material Type: Different materials require different cutting techniques. For instance, wood and metal might need substantially different equipment.
- Volume of Work: For large-scale projects, investing in more advanced machinery could prove cost-effective over time due to increased efficiency.
- Desired Precision: High precision requirements, such as in jewelry making, might demand more sophisticated cutting tools than those used in basic carpentry.
2. Factors Influencing Equipment Selection
Several factors can influence your choice of cutting equipment:
- Budget: Determine how much you can spend on cutting tools. Industrial equipment often comes at a higher price but can yield significant returns on investment.
- Space Constraints: Equipment size matters. Consider where you will store and operate the cutting tools.
- User Skill Level: Some equipment demands higher skill levels. Ensure that the users are adequately trained for the chosen tools.
3. Comparison of Materials and Brands
When choosing cutting equipment, it’s important to compare materials and brands. Look beyond the price to evaluate durability, warranty, and customer reviews. Notable brands often offer advanced features or improved ergonomics, which can justify a higher price.
Conducting a side-by-side comparison of features like blade material, sharpness, and safety features can help in making an informed decision.
Best Practices for Using Cutting Equipment Safely
1. Essential Safety Gear and Equipment
Safety should be the utmost concern when working with cutting equipment. The following gear should be mandatory:
- Protective Eyewear: Prevents eye injuries from flying debris.
- Cut-Resistant Gloves: Protect the hands from cuts and abrasions.
- Ear Protection: Reduces the risk of hearing loss when using loud machinery.
2. Safe Operating Procedures
Follow these procedures to ensure safe operation of cutting equipment:
- Always read the manufacturer’s instructions before using new equipment.
- Keep work areas tidy and free from hazards.
- Secure materials properly before cutting to minimize movement and risk.
3. Maintenance Tips for Longevity
Proper maintenance can extend the life of your cutting equipment:
- Regularly sharpen blades and replace worn parts.
- Clean tools after each use to remove debris that can cause degradation.
- Store equipment in a dry, safe place to prevent damage.
Innovative Cutting Equipment Technologies
1. Advancements in Cutting Equipment Design
Technological advancements have led to the development of cutting equipment that boasts increased efficiency and precision. For example, new CNC machines provide automated, high-speed cutting capabilities that were unimaginable a few decades ago.
Furthermore, ergonomic designs reduce operator fatigue, improving productivity and safety during prolonged use.
2. Automation and Smart Technologies
Automation has revolutionized the cutting equipment industry, allowing for tasks to be performed with minimal human intervention. Smart technologies, including IoT integrations, enable real-time monitoring and maintenance notifications, ensuring optimal performance.
3. Future Trends in Cutting Solutions
The future of cutting equipment is likely to see even more innovative solutions. Anticipated trends include:
- Increased use of AI: AI-driven systems could optimize cutting paths, significantly reducing material waste.
- Eco-friendly cutting solutions: The demand for sustainable materials and processes is driving innovation in cutting tools.
- Virtual and Augmented Reality: These technologies can be used for training operators and aiding in complex cut designs without physical prototypes.
Maximizing Efficiency with Cutting Equipment
1. Workflow Optimization Techniques
To harness the full potential of cutting equipment, consider implementing workflow optimization techniques:
- Map out the entire cutting process to identify bottlenecks and inefficiencies.
- Standardize operations to reduce variability and errors in outputs.
- Implement Lean principles to eliminate waste throughout the cutting process.
2. Measuring Performance and Productivity
Tracking performance metrics is crucial in ensuring your cutting equipment is providing value. Key performance indicators (KPIs) might include:
- Cutting speed: Measure the time taken per project to identify areas for improvement.
- Precision: Monitor tolerances to ensure cuts meet specifications consistently.
- Material waste: Evaluate how much material is discarded to identify waste reduction opportunities.
3. Case Studies of Equipment Implementation
Real-world examples of successful implementation of cutting equipment can provide invaluable insights. For instance, a manufacturing facility that invested in advanced laser cutting technology saw a 30% increase in throughput while reducing material waste by 15%. Such successes highlight the importance of selecting the right equipment tailored to specific operational needs.