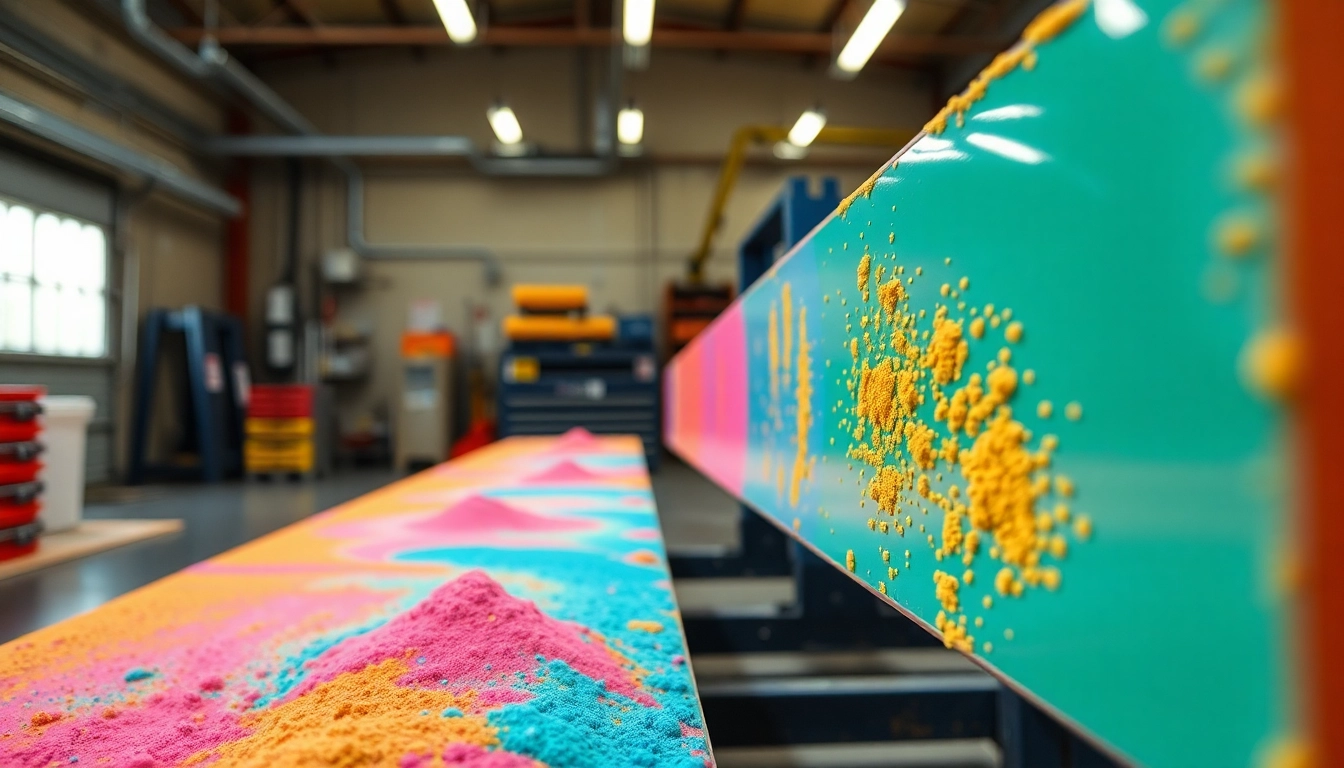
Understanding Powder Coating
What is Powder Coating?
Powder coating is a sophisticated finishing process that involves applying a dry powder to a substrate, usually metal, which is then cured under heat to create a durable, attractive finish. Unlike traditional paint applications that utilize solvents and require several layers and drying times, powder coating relies on a free-flowing powder that forms a cohesive, uniform coating through an electrostatic process. The electrostatic charge gives the powder particles the ability to adhere to the surface, where they fuse upon heating, leading to a smooth and even finish. This technique not only enhances aesthetics but also significantly increases the durability of the coated item.
In essence, powder coating is prized for its resilient characteristics, such as exceptional abrasion resistance, UV stability, and superior corrosion protection, making it a preferred choice across various industries, including automotive, furniture, and industrial manufacturing.
History and Evolution of Powder Coating
The roots of powder coating date back to the 1950s when it was first developed as a means to create a more environmentally friendly alternative to traditional liquid paint. As manufacturers were seeking solutions to reduce volatile organic compounds (VOCs), powder coating began to gain popularity. Early applications were limited due to the lack of efficient curing technologies, but advancements throughout the 1960s and 70s revolutionized the process.
By leveraging electrostatic spraying technology and improved curing ovens, the powder coating process became more efficient and effective. Initially used for industrial applications, the technology has expanded into consumer goods and decorative finishes, ranging from bicycle frames to kitchen appliances. The advancements in color pigments and texturing techniques have further diversified the applications of powder coating, ensuring its continued relevance and growth in the finishing industry today.
Benefits of Using Powder Coating
Powder coating presents an array of benefits, making it an increasingly popular choice among manufacturers and consumers alike:
- Durability: Powder-coated surfaces are highly resistant to chipping, scratching, and fading, which is crucial for items exposed to harsh environmental conditions.
- Environmental Impact: Since it emits virtually no VOCs and produces minimal waste, powder coating is considered a green technology.
- Variety of Finishes: Available in a wide range of colors and textures, powder coating allows for creativity and customization in product design.
- Cost Efficiency: While the upfront cost may be higher than traditional painting, the long-term benefits of durability and reduced maintenance needs make it a cost-effective solution.
- Simplified Application Process: With fewer steps needed compared to traditional liquid paints, powder coating can lead to reduced production times.
Types of Powder Coating
Different Powder Coating Methods
There are primarily two types of powder coating methods: electrostatic spraying and fluidized bed coating. Each has unique applications and benefits:
Electrostatic Spraying
This is the most common application method, where the powder particles are given an electrostatic charge as they exit the spray gun. The charged particles are attracted to the grounded metal substrate, resulting in an even coating layer. This method is highly efficient, especially for complex shapes and edges.
Fluidized Bed Coating
In this method, the substrate is preheated, and then it is dipped into a bed of fluidized powder. This process allows for thicker coatings and is often used for items that require a more robust finish, such as larger components and high-durability applications.
Popular Colors and Finishes in Powder Coating
One of the standout features of powder coating is the variety of colors and finishes available. From glossy and matte to textured and metallic, manufacturers can achieve unique looks that suit different aesthetic preferences. Popular color palettes include:
- Metallics: Offering a shimmering effect, metallic coatings are commonly used in automotive applications for enhancing vehicle appeal.
- Matte Finishes: Known for their modern, sleek appearance, matte coatings are popular in furniture and home décor.
- Textured Coatings: Often utilized in industrial applications, textured finishes are designed to provide both aesthetic appeal and increased grip or durability.
- Custom Colors: Many powder coating suppliers offer custom color matching services, allowing businesses to align their products with branding strategies.
Eco-Friendly Options in Powder Coating
As businesses increasingly prioritize sustainability, the demand for eco-friendly powder coating solutions has surged. Options such as low-temperature curing powders and powders formulated with bio-based components are now widely available. Additionally, many manufacturers are investing in recycling technologies, allowing for the reuse of overspray materials, which further lowers the environmental impact.
With these advancements, powder coating continues to offer eco-friendly alternatives compared to traditional liquid paints, making it a preferred choice for environmentally-conscious organizations.
Application Techniques for Powder Coating
Preparation Steps for Metal Surface
Successful powder coating depends significantly on surface preparation. A well-prepared metal surface ensures optimal adhesion and finish quality. Key steps in preparing a metal surface for powder coating include:
- Cleaning: Remove grease, dirt, and existing coatings using solvents or degreasers.
- Cleaning Methods: Various methods can be employed, including sandblasting, chemical treatments, or mechanical cleaning, depending on the substrate’s condition.
- Surface Profiling: A roughened surface improves powder adhesion, achieved through sandblasting or grinding.
- Pre-Treatment: Applying a suitable pre-treatment, such as phosphating or anodizing, enhances corrosion resistance.
Application Process and Tips
Once the surface is prepared, the actual application of powder coating begins with the following steps:
- Setup: Ensure that the booth and equipment are clean, and that safety protocols are in place.
- Loading the Powder: Fill the powder coating gun with the selected powder. The gun settings should be adjusted according to the powder type.
- Spraying: Apply the powder coating evenly across the metal surface, maintaining a consistent distance and speed. Ensure that all areas are adequately coated.
- Curing: Transfer the coated item to a curing oven where the powder will melt and cure, typically between 350°F and 400°F (177°C – 204°C) for 10 to 30 minutes, depending on the powder specifications.
- Cooling: Once cured, allow the item to cool before handling, as the finish will harden upon cooling.
Consistency in application is key to achieving a professional finish. Adapting parameters based on specific project requirements will help avoid common pitfalls.
Common Mistakes to Avoid in Powder Coating
While powder coating is straightforward, mistakes can occur that impact the outcome. Key mistakes to avoid include:
- Inadequate Surface Preparation: Failing to thoroughly clean and profile the surface can lead to poor adhesion and finish quality.
- Overexposure to Heat: Overbaking the powder can cause discoloration or an uneven surface. Always follow the manufacturer’s curing guidelines.
- Inconsistent Coating Thickness: Uneven application can result in weak spots or surface imperfections. Use appropriate techniques to promote uniform distribution.
- Ignoring Environmental Conditions: Humidity and temperature can affect the application and curing process. Monitor conditions during the process to ensure quality results.
Cost Factors in Powder Coating
Analyzing the Price of Powder Coating Services
The cost of powder coating can vary widely based on several factors, including the type of substrate, the size of the item, and the complexity of the finish. Generally, powder coating services can range from $50 to $430 per item. Many companies offer packaged pricing for bulk orders, which can lead to significant savings. Pricing considerations should include:
- Material Costs: The type and quality of powder used can significantly affect price, as specialty powders tend to be more expensive.
- Labor Costs: The complexity of the job and preparation steps can influence labor charges. More intricate designs or larger pieces typically require more labor.
- Equipment and Maintenance: strong> The initial investment in powder coating equipment should also be factored into the overall cost for businesses looking to set up in-house operations.
DIY vs Professional Powder Coating
Many enthusiasts consider DIY powder coating as a cost-saving option. However, potential drawbacks exist. While DIY kits are available, achieving the same level of quality as professional services can be challenging due to equipment and technique differences. Professionals have the advantage of advanced spray guns, curing ovens, and surface preparation technologies that contribute to superior finishes.
For individuals or small businesses weighing their options, assessing project scope and desired quality is essential. DIY might be cost-effective for simple projects but often leads to regrets for larger, more complex items where professional expertise pays off in the final finish.
Value for Money: Is Powder Coating Worth It?
Investing in powder coating offers long-term benefits that often outweigh the initial costs. The durability and low maintenance needs of powder-coated items, particularly in harsh environments, lead to fewer replacements and refinishing costs over time. Additionally, the aesthetic appeal and versatility of finishes can enhance product value, making powder coating a valuable option for manufacturers and consumers alike.
With its remarkable performance and increasing demand across various industries, powder coating is not merely a trend but a proven method of enhancing the longevity and attractiveness of many products. The return on investment becomes evident when evaluating the full lifecycle of coated items.
Future Trends in Powder Coating
Innovations in Powder Coating Technology
As technology continues to evolve, so does the powder coating industry. Notable trends include:
- Advanced Application Technologies: Innovations in electrostatic application techniques are improving efficiency and quality, allowing for better coverage and less overspray.
- Smart Powder Coatings: The emergence of smart coatings that can change color or offer additional protective features is enhancing the appeal and functionality of powder-coated surfaces.
- Focus on Sustainability: Continued advancements to reduce waste and improve the recyclability of powder will drive growth in eco-conscious markets.
- Customization Technologies: Enhanced capabilities for color matching and bespoke finishes are becoming more available, catering to market demand for personalization in products.
Market Growth and Consumer Demand for Powder Coating
The global powder coating market is projected to maintain steady growth, fueled by increasing applications in automotive, construction, and consumer goods industries. The combination of superior performance, aesthetic flexibility, and environmental benefits positions powder coating favorably amid tightening regulations on traditional paint applications.
With consumers becoming more eco-aware, opting for high-performance and low-impact finishes is likely to propel the adoption of powder coating methods. Embracing this trend will allow organizations to enhance their market competitiveness while supporting global sustainability efforts.
Advantages of Powder Coating in Various Industries
Powder coating serves multiple industries with diverse applications:
- Automotive: Enhancing the durability and aesthetics of vehicles, powder coating is critical in the automotive sector for parts such as wheels and frames.
- Furniture: Offering a wide range of colors and textures, powder coating enhances the design aesthetic while ensuring longevity against wear and tear.
- Construction: Used for architectural and structural components, powder coatings provide exceptional resistance to the elements, extending the service life of constructions significantly.
- Consumer Products: From electronics to home appliances, the appeal of powder-coated finishes ensures improved durability and design coherence across product lines.
As sustainability becomes imperative, powder coating stands out as a preferred solution across these industries, ensuring compliance while appealing to environmentally-conscious consumers.