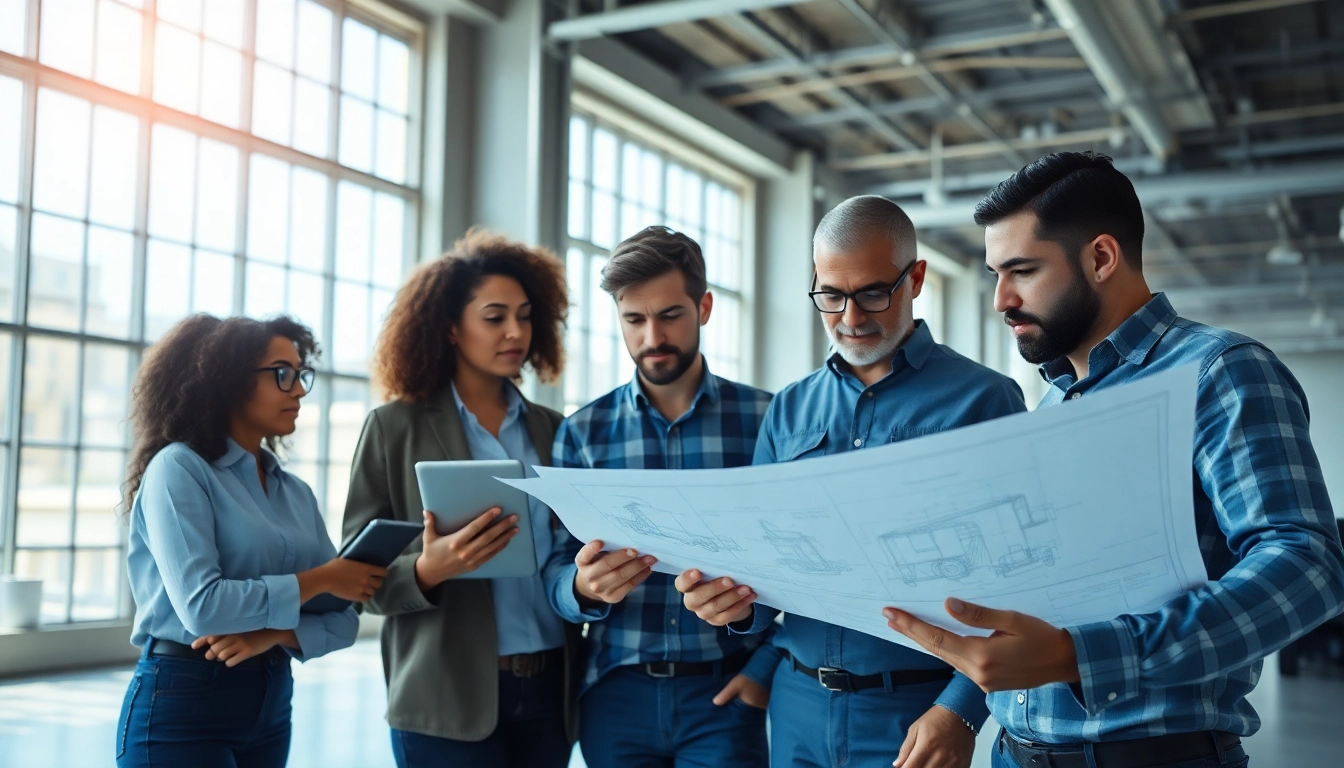
Understanding Piping Stress Analysis
What is Piping Stress Analysis?
Piping stress analysis is a critical engineering process that involves assessing the stresses imposed on piping systems in various conditions. The analysis determines how piping systems react to internal and external forces, including pressure, temperature changes, and environmental conditions. The primary goal is to ensure that the piping systems are safe, reliable, and capable of withstanding operational demands.
During this process, engineers utilize a comprehensive suite of methodologies and tools to model the physical behavior of piping networks. By simulating various scenarios, a piping stress analysis company can predict potential failures, assess safety margins, and design effective solutions to mitigate risks.
Importance of Stress Analysis in Engineering
The significance of piping stress analysis cannot be overstated. In sectors such as oil and gas, chemical processing, and power generation, the integrity of piping systems is paramount. A failure in these systems can lead to catastrophic accidents, financial losses, and environmental damage. Piping stress analysis plays a vital role in ensuring compliance with international codes and standards, protecting both personnel and assets.
Moreover, by identifying potential issues before they cause failures, companies can save on costly repairs and downtime, enhancing operational efficiency. Compliance with regulations like ASME B31.3 or API 650 not only ensures safety but also bolsters a company’s reputation and trustworthiness.
Key Terminology in Piping Stress Analysis
To navigate the complexities of piping stress analysis, several key terms and concepts are essential:
- Stress: The internal resistance offered by a material against deformation, expressed in pounds per square inch (PSI).
- Strain: The deformation of a material relative to its original length, often used to assess the degree of stress a material has undergone.
- Thermal Expansion: The change in length of the piping system due to temperature fluctuations, requiring careful calculation to prevent structural failure.
- Load Cases: Various conditions under which the piping system will operate, including dead loads, live loads, thermal loads, and seismic loads.
- Fatigue: The weakening of a material caused by repeatedly applied loads, leading to gradual damage over time.
Common Challenges Faced by Piping Stress Analysis Companies
Addressing Thermal Expansion Issues
Thermal expansion poses one of the most significant challenges in piping stress analysis. As temperatures rise, materials expand, and if this expansion is not adequately accounted for, it can lead to undue stress and even ruptures. Companies must employ precise calculations and design considerations, such as expansion joints and flexible fittings, to manage these stresses effectively.
Mitigating Vibration Effects
Vibrations in piping systems can arise from various sources, such as pumps, compressors, and even environmental factors. These vibrations can contribute to wear and tear, leading to premature failure. Piping stress analysis companies employ vibration analysis techniques to identify stress points and implement dampening solutions, such as vibration isolators and strategic supports.
Managing Load Distributions
Proper load distribution is essential in ensuring the structural integrity of piping systems. Uneven load distribution can lead to stress concentration, which enhances the risk of failure. Using advanced modeling techniques, stress analysis companies can predict load behaviors under different scenarios, optimizing support locations and pipe routing to evenly distribute stresses.
Best Practices for Effective Piping Stress Analysis
Choosing the Right Analysis Tools
The choice of analysis tools is crucial for achieving accurate results in piping stress analysis. Advanced simulation software, such as CAE (Computer-Aided Engineering) tools, allow engineers to create detailed models that simulate real-life operating conditions. These tools enable comprehensive scenario testing and sensitivity analyses to inform design choices and strategies.
Conducting Comprehensive Surveys
Before initiating any analysis, conducting thorough surveys is imperative. Understanding the physical environment, existing structures, and potential external forces ensures that all relevant factors are included in the analysis. Field data collection, including temperature readings and pressure measurements, provides a solid foundation for accurate modeling.
Implementing Regular Maintenance Protocols
Maintenance is often overlooked in stress analysis. Regular inspections and maintenance protocols can identify wear and tear early, allowing for timely interventions before serious issues arise. Establishing a culture of preventive maintenance ensures that piping systems remain within safe operating parameters throughout their lifecycle.
Case Studies: Successful Piping Stress Analysis Projects
Project Overview: Critical Infrastructure
A real-world example is a recent project undertaken for a major oil refinery. The facility faced significant challenges with thermal expansion due to the extreme temperature variations of the substances being processed. The piping stress analysis company implemented innovative expansion loop designs and incorporated flexible piping arrangements. This resulted in the successful operation of the facility without any incidents over the last five years.
Lessons Learned from Complex Projects
Through experience, one key lesson learned is the importance of multi-disciplinary collaboration. During a project involving multiple engineering disciplines (mechanical, civil, and electrical), regular coordination meetings ensured that design choices aligned across teams. This approach minimized conflicts and enhanced the overall integrity of the system.
Client Testimonials on Our Services
Clients have lauded the comprehensive nature of the analysis provided. For instance, a major chemical plant noted that the in-depth stress assessments enabled them to avoid costly emergency repairs thanks to predictive recommendations made before issues escalated. Such testimonials highlight the value of thorough piping stress analysis and its impact on operational safety and efficiency.
The Future of Piping Stress Analysis
Emerging Technologies in Stress Analysis
The field of piping stress analysis is evolving rapidly, with emerging technologies such as artificial intelligence and machine learning enhancing predictive capabilities. These technologies facilitate complex data analysis that can inform preemptive actions, improving safety and resource allocation.
Trends in Hydraulic Modeling
Hydraulic modeling continues to grow in importance. With the push towards smart infrastructure, conducting accurate hydraulic analysis helps simulate various flow regimes and ensure the efficient operation of piping systems. Enhanced modeling techniques allow for better prediction of fluid dynamics, ultimately impacting the design decisions made during piping layout and construction.
Impact of Regulations on Engineering Practices
Regulatory changes frequently shape the operational landscape for piping stress analysis companies. Staying abreast of evolving standards, such as those set forth by the American Society of Mechanical Engineers (ASME) and the International Organization for Standardization (ISO), is necessary for compliance and safety. Proactively adapting to these changes in practice ensures the longevity and safety of piping systems.