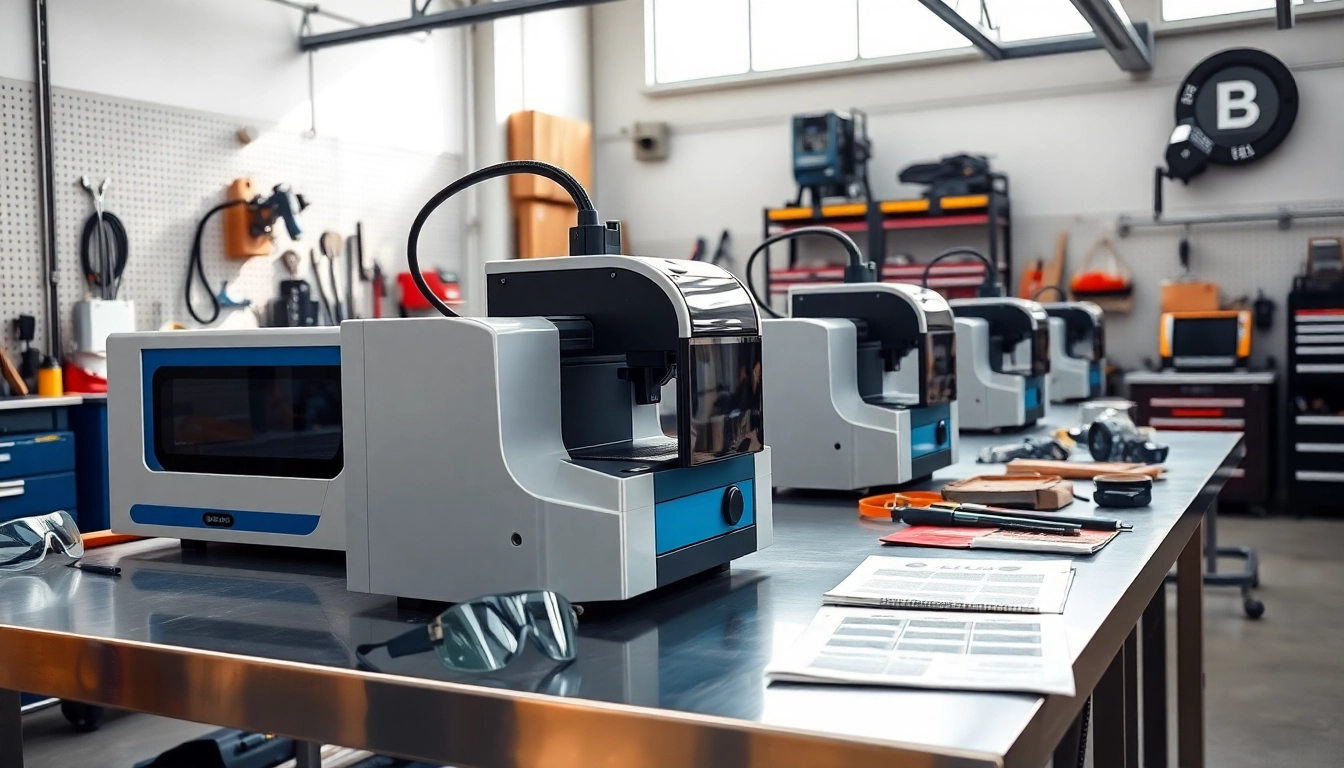
Understanding the Basics of Cutting Equipment
In the realm of industrial manufacturing, the efficacy and precision of operations often hinge on the type of cutting equipment employed. Cutting equipment encompasses a broad array of tools and machines designed to slice through materials ranging from metals to composites. Selecting appropriate cutting equipment can significantly enhance production efficiency, reduce waste, and ensure product quality. This article will delve into the fundamentals of cutting equipment, helping you understand its various functions and applications.
Types of Cutting Equipment Available
There are several types of cutting equipment, each tailored for specific materials and applications. Below are some commonly used types:
- Laser Cutting Machines: These machines utilize focused laser beams to cut a wide variety of materials with high precision. They are ideal for intricate designs and can cut through thick materials.
- Waterjet Cutters: Waterjet cutting employs high-pressure water jets, often mixed with abrasives, to slice through hard materials like stone and metals. It is a versatile method applicable to both delicate and robust items.
- Plasma Cutters: Plasma cutting uses a focused plasma arc to melt and remove material. It’s efficient for cutting metals such as steel and aluminum and is favored in industries requiring rapid production.
- Band Saws: Ideal for cutting hard materials, band saws are versatile and can be used for both straight and curved cuts. They are commonly used in lumber and metal processing.
- Angle Cutters: These tools are designed to make bevel and angle cuts on various materials, providing flexibility in design and functionality.
How Cutting Equipment Functions
Understanding the operational principles behind cutting equipment is crucial to maximizing its utility:
- Laser Cutting: By emitting a concentrated beam of light, the equipment heats the material’s surface to the point of melting or vaporization, allowing for precision cuts.
- Waterjet Cutting: The equipment uses a high-velocity jet of water, sometimes mixed with abrasives, to erode the material, producing accurate cuts without heating the material, which helps maintain structural integrity.
- Plasma Cutting: Utilizing a stream of ionized gas, plasma cutters create high-temperature arcs that melt the material and blow away the molten metal, resulting in clean edges.
- Band Saws: These saws have a continuous band of toothed metal that rotates around two or more wheels. The linear motion of the blade through the material provides flexibility for various cuts.
- Angle Cutters: They use rotating blades to cut at designated angles, allowing for the creation of specific designs and shapes as required by the project.
Key Features to Look For
When selecting cutting equipment, several key features can be pivotal in determining its performance and suitability:
- Cutting Speed: The speed at which the equipment can operate affects overall productivity. Faster machines can increase output but may sacrifice precision if not properly calibrated.
- Precision: The accuracy of the cut is critical, especially for industries requiring stringent tolerances. Advanced equipment often includes features that enhance precision, such as CNC technology.
- Ease of Use: User-friendly interfaces and intuitive controls enhance operational efficiency and reduce training time for workers.
- Durability: Machines that can withstand heavy usage and adverse conditions tend to have longer lifespans and lower maintenance costs.
- Safety Features: Considering equipment equipped with safety measures such as automatic shut-off systems or protective covers ensures a safer working environment.
Identifying Your Specific Cutting Needs
Understanding your specific cutting needs is essential to choosing the right equipment. Consider the following factors:
Assessing Material Types and Thickness
The materials you’ll be cutting play a significant role in your equipment selection. Different materials require different approaches:
- Metals: Steel and aluminum, for example, often require plasma or laser cutters capable of handling their thermal properties.
- Wood: A band saw is typically better suited for lumber due to its blade design, which can handle the fibrous nature of wood.
- Composites: Materials like carbon fiber may necessitate waterjet cutting to prevent delamination.
Thickness also matters. Thicker materials generally require more powerful cutting solutions, such as high-output lasers or bandsaws equipped for heavy cutting.
Understanding Production Volumes
Production volume dictates the type and scale of equipment necessary to meet demands:
- Low Volume/High Customization: For low batch sizes with frequent design alterations, versatile equipment such as laser cutters may be more beneficial.
- High Volume Production: When your production runs are large and consistent, investing in automated systems that maximize throughput, like CNC machining centers, might be the most efficient route.
Examining your usual order sizes and frequency will help define whether you need flexible machinery or highly specialized equipment.
Considering Safety Features
Safety should never be overlooked. Each type of cutting equipment comes with potential hazards, making safety features a priority:
- Emergency Stop Mechanisms: Ensure your equipment has clear and accessible emergency controls.
- Protective Guards: Machines should include shields or covers that protect operators from flying debris and accidental contact.
- Operator Training: Adequate training on safety protocols and machine operation is essential for preventing accidents and injuries.
Top Brands in Cutting Equipment
The following brands are recognized as leaders in the cutting equipment market, known for their innovation, reliability, and customer support:
Popular Cutting Equipment Manufacturers
Some prominent manufacturers in the cutting equipment industry include:
- TRUMPF: Known for high-performance laser cutting systems utilized in multiple sectors, including automotive and aerospace.
- Hypertherm: A leader in plasma cutting technologies, Hypertherm designs reliable tools with a focus on precision and efficiency.
- JET: JET’s line of band saws and workshop tools is known for durability and cost-effectiveness, catering to both hobbyists and professional users.
- Esab: Specializes in high-quality welding and cutting equipment, offering advanced solutions that meet diverse industrial requirements.
- Flow International: A mainstay in the waterjet cutting segment, Flow International is known for its mission-critical systems across various materials.
Comparing Performance and Reliability
When evaluating cutting equipment, it’s important to measure performance against reliability:
- Performance Metrics: High-speed capabilities, precision metrics, and cutting range are all essential data points that should guide your comparisons.
- Reliability: Researching the mean time between failures (MTBF) can provide insight into a machine’s durability. Equipment with lower maintenance frequency generally offers better long-term reliability.
Reading product specifications, user forums, and technical manuals can enhance your understanding of each model’s performance and limitations.
Market Reviews and Testimonials
Customer reviews are invaluable for gauging real-world performance:
- Seek testimonials from businesses within your industry to understand how the equipment performed under similar conditions.
- Consider rating websites and forums where users share their experiences and challenges. This feedback can guide you in recognizing potential pitfalls or advantages.
Best Practices for Selecting Cutting Equipment
Choosing cutting equipment entails careful consideration. Here are best practices to follow:
Evaluating Cost vs. Value
Many factors influence the cost of cutting equipment, from brand reputation to technological innovations. To ensure a worthwhile investment:
- Initial Cost vs. Total Cost of Ownership: Consider both the purchase price and ongoing operational costs, including maintenance, parts, and energy consumption.
- Value Assessment: Evaluate how the equipment will improve productivity and quality, thereby enhancing your overall return on investment (ROI).
Researching and Comparing Options
A comprehensive comparison of options is paramount. Use a systematic approach:
- Identify Needs: Clearly outline the specifics of your cutting needs and match them against available options in the market.
- Screen Candidates: Create a shortlist of equipment that meets surface-level criteria, then delve deeper into technical specifications and performance capabilities.
Consulting Industry Professionals
Leverage the wisdom of industry experts to corroborate your research. Discussions with consultants, equipment suppliers, and peers can provide deeper insights:
- Networking: Attend trade shows and industry events where you can engage directly with manufacturers and other experts.
- Online Forums: Participate in online communities where industry professionals discuss their experiences with specific equipment.
Maintaining Your Cutting Equipment for Longevity
Proper maintenance is critical to prolonging the lifespan and enhancing the performance of cutting equipment. Here are key practices:
Regular Maintenance Procedures
Implementing a structured maintenance schedule is essential:
- Routine Inspections: Check for signs of wear and tear, ensuring that all parts function correctly without excessive play.
- Cleaning: Regularly clear debris and build-up that may affect performance. Ensure that optics, in the case of laser cutters, are clean to maintain cutting accuracy.
- Software Updates: Keep the machine’s software up to date for optimal performance and to benefit from latest features and security patches.
Signs Your Equipment Needs Repair
Be alert for warning signs indicating your machine may require service:
- Inconsistent Cuts: Changes in cut quality or precision often indicate a need for calibration or maintenance.
- Excessive Heat: Equipment generating unusual heat levels may be overworking or malfunctioning.
- Noisy Operation: Grinding or unusual noises from cutting equipment can signal alignment issues or worn parts.
Tips for Extending Equipment Lifetime
Here are several proactive ways to ensure your cutting equipment remains in optimal condition:
- Train Operators: Ensure that all personnel handling the equipment are adequately trained in operation and safety protocols.
- Invest in Quality: While it may be tempting to opt for cheaper options, high-quality equipment typically offers better durability and lower long-term costs.
- Maintain Spare Parts Inventory: Keeping an inventory of critical components can minimize downtime when repairs are necessary.