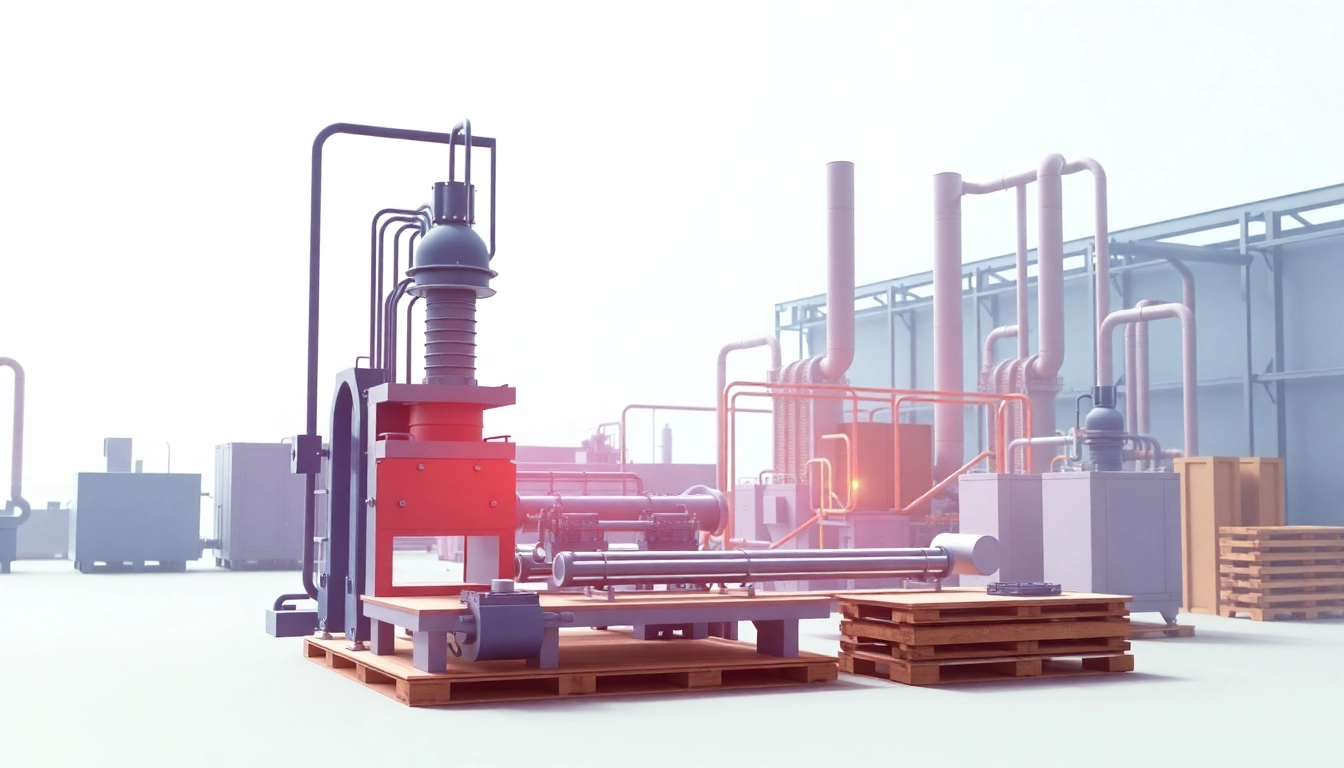
Essential Features of Liquid Packaging Machines
Liquid packaging machines are essential tools in various industries, such as food, beverage, pharmaceuticals, and chemicals. They are designed to efficiently fill, seal, and package liquids into various types of containers. The effectiveness and reliability of these machines are paramount to ensure product quality and safety. Understanding the essential features of liquid packaging machines can help companies choose a suitable supplier, like a Liquid Packaging Machine Supplier, who meets their specific needs.
1. Types of Liquid Packaging Machines
Liquid packaging machines come in various forms, each tailored to meet the diverse requirements of different products and industries. Here are some common types of liquid packaging machines:
- Filling Machines: These machines fill liquids into containers. They can be further categorized into gravimetric, volumetric, and piston fillers, depending on the specific needs of the product.
- Capping Machines: Once the liquid is filled, capping machines seal the containers to prevent leakage and contamination. They range from manual to automated machines.
- Labeling Machines: These machines apply labels to containers, which is essential for branding and regulatory compliance.
- Pouch Fillers: Used for liquids that are packaged in flexible pouches, these machines are often employed in the food industry for sauces, drinks, and liquid snacks.
- Baggers: Used for bulk liquids, these machines package liquids in pre-formed bags and are common in chemical and industrial applications.
2. Key Technologies in Liquid Packaging
Modern liquid packaging machines leverage advanced technologies to enhance efficiency and accuracy. Some key technologies include:
- Automation and Robotics: Automated systems expedite the packaging process and minimize human error, thereby boosting overall efficiency.
- Smart Sensors: Sensors can monitor fill levels, detect leaks, and ensure packages are sealed correctly, increasing product safety and quality.
- Data Collection and Analytics: Modern machines are equipped with data collection features that allow for real-time performance monitoring, aiding in predictive maintenance and process optimization.
- Flexible Packaging Options: Many machines now offer the ability to handle multiple types and sizes of containers, allowing businesses to adapt quickly to market changes.
3. Advantages of Automated Packaging Systems
Investing in automated liquid packaging systems offers numerous advantages:
- Increased Efficiency: Automated systems reduce downtime between operations, enabling manufacturers to achieve higher throughput rates.
- Improved Precision: Automated machines offer consistency in filling accuracy and container handling, reducing waste and ensuring compliance with regulations.
- Enhanced Safety: Automation minimizes the risk of accidents that can occur with manual operations, fostering a safer workplace environment.
- Cost Savings: While the initial investment in automated machines may be higher, they typically offer lower operational costs and faster return on investment through increased productivity.
Choosing the Right Liquid Packaging Machine Supplier
Selecting a reliable liquid packaging machine supplier is critical to the success of your packaging operations. A good supplier should not only provide high-quality machines but also offer valuable support throughout the purchasing and operational phases.
1. Evaluating Supplier Credentials
Begin your supplier search by evaluating their credentials. Consider the following:
- Experience: Look for suppliers with a proven track record in the liquid packaging industry. Experienced suppliers are likely to have tackled various challenges and developed effective solutions.
- Certifications: Certifications such as ISO or those related to health and safety standards can indicate a commitment to quality and reliability.
- Client Testimonials: Reviews and testimonials from previous clients can provide insights into the supplier’s reliability and level of customer service.
2. Comparing Performance and Reliability
Performance metrics can significantly influence your choice of supplier:
- Machine Efficiency: Examine the operational efficiency rates of the machines offered by the supplier to ensure they meet your production needs.
- Downtime Statistics: A supplier with low downtime statistics indicates reliable equipment that is integral for continuous production.
- Support Services: Ensure the supplier offers strong technical support and maintenance services to minimize disruptions during operations.
3. Understanding Warranty and Support Services
Before making a final decision, it’s crucial to understand the warranty and support services provided by the supplier:
- Warranty Terms: A solid warranty protects your investment and indicates the supplier’s confidence in their machines.
- Post-Purchase Support: Check for training availability, service contracts, and support response times to resolve issues quickly and efficiently.
Benefits of Custom Liquid Packaging Solutions
Custom liquid packaging solutions offer tailored advantages to businesses in need of unique packaging processes. These solutions not only streamline operations but also contribute to better product quality.
1. Tailoring Machines for Specific Industries
Each industry has its unique requirements. Custom machines can be tailored to suit:
- Viscosity Considerations: For viscous liquids like gels or creams, customized filling machines can be designed to manage thick textures without collapsing the product integrity.
- Product Sensitivity: Sensitive products, such as pharmaceuticals, may require specific handling mechanisms to maintain sterility and quality.
- Packaging Formats: Custom solutions can also accommodate various container shapes and sizes, allowing brands to differentiate themselves in a competitive market.
2. Enhancing Productivity with Specific Designs
Custom packaging machines can significantly boost productivity:
- Optimized Workflows: Designs that match specific production workflows reduce bottlenecks, leading to more efficient operations.
- Integrated Systems: A machine tailored to work within an integrated packaging line can streamline processes, reducing handling time and labor costs.
3. Cost Efficiency Through Custom Solutions
While customized solutions may seem more costly upfront, they can result in long-term financial benefits:
- Reduction in Waste: Machines designed for specific liquids result in fewer spills and wasting of materials, thus minimizing costs over time.
- Higher Production Rates: Custom solutions are designed to maximize output, which can be a significant cost-saving factor in large-scale operations.
Maintenance and Care for Liquid Packaging Machines
Proper maintenance of liquid packaging machines is crucial to ensure longevity, reliability, and consistent performance.
1. Routine Maintenance Tips
Implementing a regular maintenance schedule will help in prolonging the life of your machines:
- Regular Cleaning: Regularly clean the machines to avoid contamination of liquids and maintain hygienic standards.
- Lubrication: Ensure that all moving parts are adequately lubricated to prevent wear and tear.
- Calibration: Frequently calibrate machines to ensure fill levels and seal integrity meet operational standards.
2. Troubleshooting Common Issues
Understanding common issues can help your team address them swiftly:
- Fill Level Inconsistency: Check for blockages and ensure the dosing mechanism is calibrated correctly.
- Poor Sealing: Inspect the sealing mechanisms and ensure the correct materials are used and temperatures are monitored.
- Label Misalignment: Ensure that labeling machines are correctly aligned to avoid costly errors in branding and compliance.
3. Importance of Regular Inspections
Conducting regular inspections is vital to catch and fix issues before they become detrimental to production:
- Scheduling Inspections: Create a maintenance calendar that includes daily, weekly, and monthly inspections.
- Training Staff: Train staff to identify potential problems and respond appropriately to ensure minimal downtime.
The Future of Liquid Packaging Technology
As industries continue to evolve, so do the technologies applied in liquid packaging. Staying informed about new trends helps businesses adapt and remain competitive.
1. Innovations and Trends in the Industry
The liquid packaging industry is witnessing several innovations:
- Use of AI and Machine Learning: Advanced analytics and AI are improving predictive maintenance and operational efficiency.
- Smart Packaging: Innovations include packaging that can communicate with consumers and provide enhanced product information.
- Modular Systems: Machines that can be easily upgraded or customized as market needs change offer flexibility and longevity.
2. Sustainability Efforts in Packaging
Sustainability is a critical area of focus for manufacturers:
- Eco-Friendly Materials: Many packaging companies are investing in biodegradable and recyclable materials to reduce environmental impact.
- Energy Efficiency: New packaging machines are being designed to use less energy during operation, contributing to lower carbon footprints.
3. Adapting to Market Demands
Staying ahead in a rapidly changing market requires adaptability:
- Customization: Embracing custom solutions can help brands meet unique consumer demands and preferences.
- Speed to Market: As trends shift, the ability to quickly adapt packaging lines can give businesses a competitive edge.