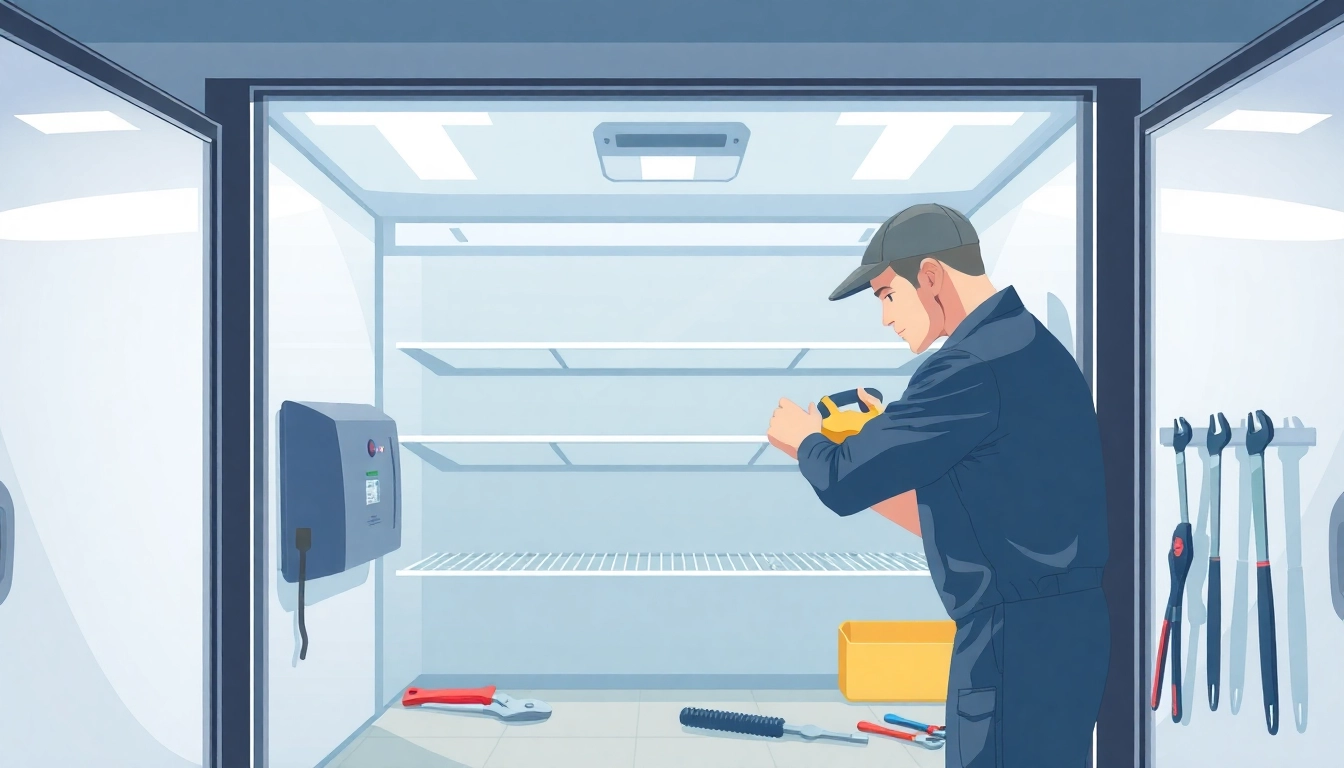
Understanding Walk in Freezer Repair
Walk-in freezers are essential components for many businesses, providing the necessary refrigeration for food storage and other perishable items. When they malfunction, not only can it lead to significant food spoilage and loss, but it can also impact overall business operations. For reliable solutions, consider exploring walk in freezer repair services that can get your unit back in working order efficiently.
Common Issues with Walk in Freezers
Understanding the common problems associated with walk-in freezers is crucial for timely repairs and effective maintenance. Here are some prevalent issues:
- Thermostat Malfunctions: A faulty thermostat can prevent the freezer from reaching and maintaining the desired temperatures.
- Compressor Problems: The compressor is the core of the refrigeration cycle. If it fails, the freezer cannot cool effectively.
- Condenser Coil Blockage: If dust and debris clog the condenser coils, the efficiency drops, leading to increased energy consumption and potential system failure.
- Evaporator Coil Freezing: Poor airflow or a refrigerant leak can cause the evaporator coils to freeze, obstructing the cooling process.
Signs You Need Professional Repair
Many business owners may overlook early warning signs of freezer issues. Recognizing these signs promptly can help prevent costly repairs down the line:
- Unusual Noises: If your freezer is making strange sounds like buzzing or clanging, it could indicate mechanical issues.
- Poor Cooling Performance: Inconsistent temperatures, particularly above freezing, often signal compressor or refrigerant problems.
- Frequent Cycling: Repeatedly turning on and off can suggest issues with the compressor or thermostat.
- Condensation Issues: Excess moisture on the interior or exterior indicates a failure in insulation or condensation drainage.
The Importance of Timely Maintenance
Regular maintenance of walk-in freezers is essential for ensuring optimal performance and longevity. Neglecting maintenance can lead to severe breakdowns and costly emergency repairs. Businesses should implement a routine maintenance schedule that includes:
- Inspection and cleaning of condenser and evaporator coils.
- Checking door seals and gaskets for leaks.
- Monitoring refrigerant levels and identifying leaks.
- Testing the thermostat and calibration as needed.
Identifying Walk in Freezer Problems Early
Temperature Fluctuations: A Red Flag
Temperature inconsistencies are one of the most apparent indicators that your walk-in freezer needs attention. Understanding the causes can help you troubleshoot effectively:
- Thermostat settings may be incorrect or malfunctioning.
- There might be a refrigerant leak, causing failure in maintaining desired temperatures.
- Blocked evaporator coils could disrupt airflow, leading to uneven cooling.
Noisy Operation: What It Means
Noises that are out of the ordinary can indicate mechanical failures. Common sounds and their implications include:
- Banging or Clanging: May signify loose components within the compressor or fan.
- Buzzing: Can indicate electrical issues or a failing compressor.
- Hissing: Often points to a refrigerant leak.
Ice Buildup: Causes and Solutions
Ice accumulation inside a walk-in freezer can hamper efficiency and airflow. Causes of ice buildup might include:
- Dirty evaporator coils leading to reduced efficiency.
- High humidity and poor ventilation causing condensation to freeze.
- Faulty door seals allowing warm air to enter.
Solutions involve annually cleaning coils, inspecting door seals, and ensuring proper ventilation.
Choosing the Right Repair Service
What to Look for in a Repair Technician
When selecting a repair technician for your walk-in freezer, consider the following:
- Experience and Certifications: Choose technicians with relevant experience and certifications in commercial refrigeration.
- Availability: Ensure the technician offers prompt service, especially in emergencies.
- Comprehensive Service: Look for companies providing a full range of repair, maintenance, and emergency services.
Comparing Service Offers
Before committing to a repair service, compare multiple offers. This assessment should include:
- Pricing structures—consider both upfront and hidden costs.
- Range of services offered—ensure they address your specific freezer issues.
- Warranty and customer support—a quality service should offer warranties on both parts and labor.
Customer Reviews and Recommendations
Researching customer reviews can provide valuable insights into a company’s reliability and service quality. Look for feedback regarding:
- Timeliness and responsiveness of service.
- Effectiveness of repairs performed.
- Overall customer satisfaction.
Preventive Maintenance for Walk in Freezers
Regular Inspections and Tune-Ups
Establishing a routine for inspections allows business owners to catch minor problems before they evolve into major repairs. Schedule routine checks for:
- Electrical connections and housing.
- Structural integrity of the freezer.
- Performance of mechanical components.
Cleaning and Upkeeping Components
Routine cleaning of various components not only boosts performance but also prolongs the equipment’s lifespan. Key areas include:
- Condenser Coils: Should be cleaned every few months to prevent overheating.
- Evaporator Coils: Must be accessed and cleaned to ensure proper airflow.
- Door Seals: Should be inspected and replaced if worn out to maintain efficiency.
Seasonal Maintenance Tips
Seasonal changes can affect the performance of walk-in freezers. Keep the following tips in mind:
- Before summer, check the cooling system, ensuring it can handle higher ambient temperatures.
- During winter, ensure that the external components are insulated appropriately to prevent freezing in cold conditions.
- Update maintenance schedules to accommodate busy seasons, including pre-holiday checks.
Cost Considerations for Walk in Freezer Repair
Budgeting for Repairs
Understanding the potential costs associated with walk-in freezer repairs is crucial for effective budgeting. Businesses should anticipate expenses in areas like:
- Parts replacements, which can vary significantly based on the components needed.
- Labor costs, often based on the complexity and time required for repairs.
- Potential loss of inventory during repairs that might affect your bottom line.
Cost-Effective Solutions
To minimize repair costs, businesses can consider several cost-effective strategies:
- Establishing a maintenance contract can reduce the frequency and severity of repairs.
- Keeping records of past repairs can help technicians address problems more quickly, reducing labor time.
- Implementing energy-efficient practices can prevent excess wear and tear on equipment, leading to reduced repair needs.
Understanding Rate Differences among Service Providers
Service rates can vary dramatically between providers. Factors influencing these rates include:
- Location: Rates may differ based on geographic areas, with urban areas typically charging more.
- Technician Expertise: Highly qualified technicians may demand higher rates, but their experience can lead to more efficient problem-solving.
- Service Readiness: Companies offering 24/7 emergency service may charge a premium for immediate response.